Method for preparing difluoroethanol by gas phase catalytic hydrogenation
A difluoroethanol, catalytic hydrogenation technology, applied in chemical instruments and methods, preparation of hydroxyl compounds, preparation of organic compounds, etc., can solve the problem of low conversion rate of difluorocarboxylate, unsuitable for industrial production, unfavorable industrial production The problem is to overcome the harsh reaction conditions, low cost and low equipment requirements.
- Summary
- Abstract
- Description
- Claims
- Application Information
AI Technical Summary
Problems solved by technology
Method used
Examples
Embodiment 1
[0030] CuO / ZnO / Al 2 o 3 / La (the molar ratio of Cu, Zn, Al, and La is Cu:Zn:Al:La=1:0.5:0.5:0.1) catalyst 3g is placed in a stainless steel gas phase reaction tube with a diameter of 10mm and 316L, and heated to 150°C Introduce 10ml / min of hydrogen gas to activate the catalyst for 0.5h, and then inject methyl difluoroacetate and hydrogen gas with a molar ratio of 1:10. The reaction temperature is 150°C, the reaction pressure is normal pressure, and the space velocity is 5s. -1 The reaction is carried out under the conditions, and the reaction product is collected and rectified to obtain the product. After reacting for 1 hour, sampling and analysis were carried out at the outlet of the gas phase reaction tube. The conversion rate of methyl difluoroacetate was 90%, and the selectivity of difluoroethanol was 85%.
Embodiment 2
[0032] CuO / ZnO / Al 2 o 3 / Y (the molar ratio of Cu, Zn:, Al, Y is Cu:Zn:Al:Y=1:0.1:0.1:0.01) catalyst 3g is placed in a gas phase reaction tube with a diameter of 10mm and 316L, and heated to 270°C Introduce 10ml / min of hydrogen gas to activate the catalyst for 0.5h, and then inject ethyl difluoroacetate and hydrogen gas with a molar ratio of 1:8. The reaction temperature is 270°C, the reaction pressure is normal pressure, and the space velocity is 15s. -1 The reaction is carried out under the conditions, and the reaction product is collected and rectified to obtain the product. After reacting for 1 hour, sample analysis was carried out at the outlet of the gas phase reaction tube, the conversion rate was 89%, and the selectivity was 84.5%.
Embodiment 3
[0034] CuO / ZnO / Al 2 o 3 / Lu (the molar ratio of Cu, Zn:, Al, Lu is Cu:Zn:Al:Lu=1:1:0.3:0.05) the catalyst is placed in a gas phase reaction tube with a diameter of 10mm and 316L, heated to 290°C and passed through 10ml / min of hydrogen, after activating the catalyst for 0.5h, feed difluoropropyl acetate and hydrogen with a molar ratio of 1:6, the reaction temperature is 290°C, the reaction pressure is normal pressure, and the space velocity is 30s -1 The reaction is carried out under the conditions, and the reaction product is collected and rectified to obtain the product. After reacting for 1 hour, sample analysis was carried out at the outlet of the gas phase reaction tube, the conversion rate was 92%, and the selectivity was 90%.
PUM
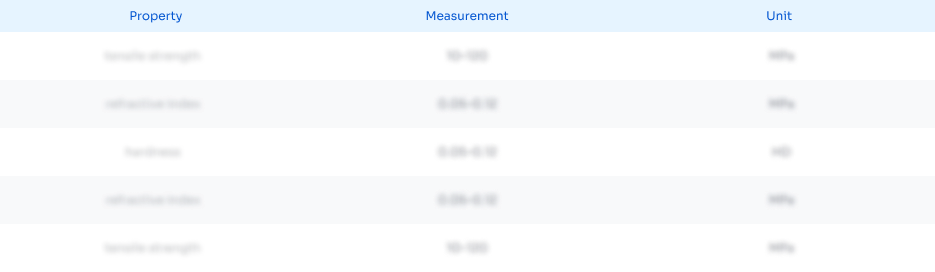
Abstract
Description
Claims
Application Information

- R&D
- Intellectual Property
- Life Sciences
- Materials
- Tech Scout
- Unparalleled Data Quality
- Higher Quality Content
- 60% Fewer Hallucinations
Browse by: Latest US Patents, China's latest patents, Technical Efficacy Thesaurus, Application Domain, Technology Topic, Popular Technical Reports.
© 2025 PatSnap. All rights reserved.Legal|Privacy policy|Modern Slavery Act Transparency Statement|Sitemap|About US| Contact US: help@patsnap.com