Medium and large casting roller ramming mould heating and feeding method and device
A technology of large and medium-sized molds, which is applied in the field of metallurgical roll casting, can solve problems such as difficult demoulding, scrapped rolls, turning tools, machine tools, man-hours, energy waste, etc., to reduce the labor intensity of demoulding, reduce smelting costs, and save The effect of the demoulding process
- Summary
- Abstract
- Description
- Claims
- Application Information
AI Technical Summary
Problems solved by technology
Method used
Image
Examples
Embodiment Construction
[0028] The present invention will be further described through the embodiments below in conjunction with the accompanying drawings.
[0029] A large and medium-sized casting roll ramming mold heating and shrinkage device, comprising an induction heating coil 1, an upper roll neck mold 2, a roll body mold 3 and a lower roll neck mold 4, the upper roll neck mold is set on The upper part of the roll body mold, the lower roll neck mold is arranged at the lower part of the roll body mold, the longitudinal axis of the roll body mold, the longitudinal axis of the upper roll neck mold and the longitudinal axis of the lower roll neck mold coincide. On a vertical straight line 9; the upper roll neck mold is separated from the roll body mold, and the upper roll neck mold is cylindrical with a large bottom and a small taper, and an induction heating coil is arranged on the outside, which is a multi-turn The coil, the induction heating coil has the same taper as the upper roll neck casting...
PUM
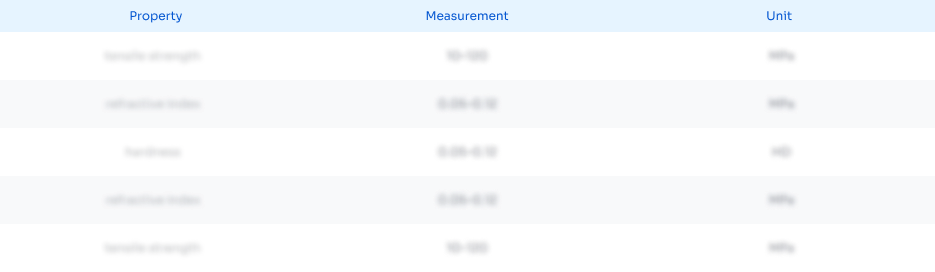
Abstract
Description
Claims
Application Information

- R&D
- Intellectual Property
- Life Sciences
- Materials
- Tech Scout
- Unparalleled Data Quality
- Higher Quality Content
- 60% Fewer Hallucinations
Browse by: Latest US Patents, China's latest patents, Technical Efficacy Thesaurus, Application Domain, Technology Topic, Popular Technical Reports.
© 2025 PatSnap. All rights reserved.Legal|Privacy policy|Modern Slavery Act Transparency Statement|Sitemap|About US| Contact US: help@patsnap.com