Coating for lost foam casting, and preparation method thereof
A lost foam casting and coating technology, which is applied to casting molding equipment, coatings, molds, etc., and can solve problems such as high cost and poor coating performance
- Summary
- Abstract
- Description
- Claims
- Application Information
AI Technical Summary
Problems solved by technology
Method used
Image
Examples
preparation example Construction
[0036] In addition, the present invention also provides a preparation method of the above-mentioned coating for lost foam casting, the preparation method comprising:
[0037] Step 1, mixing quartz sand and bauxite to obtain refractory aggregate, wherein the weight ratio of quartz sand to bauxite is 3:7 to 4:6;
[0038] Step 2, adding water to the refractory aggregate and stirring; and
[0039] Step 3, adding suspending agent and binder to the mixture of refractory aggregate and water and stirring.
[0040] Wherein, the time for stirring and mixing quartz sand and bauxite in step 1 can be determined according to actual conditions, and it is a standard to mix quartz sand and bauxite as fully as possible. Usually, the time for stirring in step 1 The time is 5min-10min; similarly, the time for stirring in step 2 can also be determined according to the actual situation, so that the quartz sand and bauxite are dispersed in water as uniformly as possible as a standard, usually, the ...
Embodiment
[0051] Coating samples 1-8 for lost foam casting were prepared according to the following steps, respectively:
[0052] Step 1. Stir and mix the components of the refractory aggregate. The components and proportions and average particle size of the refractory aggregate in samples 1-8 are shown in Table 1. During the preparation process of samples 1-8, carry out The time of stirring is shown in table 4 respectively;
[0053] Step 2: Add water to the refractory aggregate and stir, wherein the weight ratios of water and refractory aggregate in samples 1-8 are shown in Table 1, and the time of stirring during the preparation of samples 1-8 is in step 2 The time for stirring is shown in table 4 respectively; and
[0054] Step 3. Add binder and suspending agent to the mixture of refractory aggregate and water and stir, the type of binder in sample 1-8 and its ratio with refractory aggregate, and the suspending agent in sample 1-8 The types of the samples and their proportioning ra...
PUM
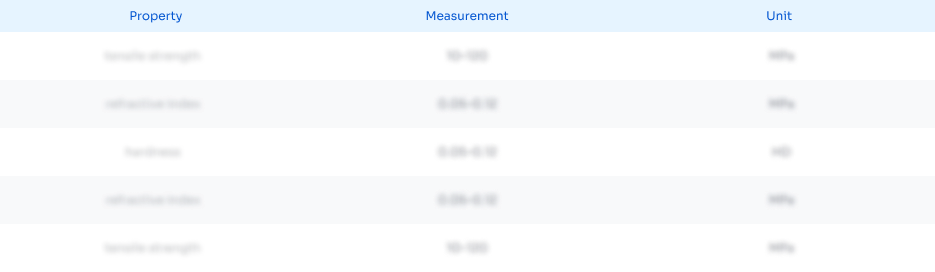
Abstract
Description
Claims
Application Information

- R&D Engineer
- R&D Manager
- IP Professional
- Industry Leading Data Capabilities
- Powerful AI technology
- Patent DNA Extraction
Browse by: Latest US Patents, China's latest patents, Technical Efficacy Thesaurus, Application Domain, Technology Topic, Popular Technical Reports.
© 2024 PatSnap. All rights reserved.Legal|Privacy policy|Modern Slavery Act Transparency Statement|Sitemap|About US| Contact US: help@patsnap.com