Beneficiation process for quality improvement and iron removal of feldspar ores
A feldspar ore and process technology, applied in flotation, solid separation, wet separation, etc., can solve the problems of large consumption, large investment of strong magnetic machine, low concentration of concentrate, etc., to reduce the cost of flotation and the scope of application Wide and selective effect
- Summary
- Abstract
- Description
- Claims
- Application Information
AI Technical Summary
Problems solved by technology
Method used
Image
Examples
Embodiment Construction
[0025] In order to further describe the present invention, the separation process for upgrading and removing iron from feldspar ore of the present invention will be described in more detail below in conjunction with examples.
[0026] The feldspar ore is taken from a feldspar mine in southern Anhui, Anhui. The ore is a weathered granite-type sand (pebble) deposit. The results of the original ore are shown in Table 1:
[0027] Table 1 Analysis results of raw ore
[0028] Raw ore composition K 2 o Na 2 o Fe 2 o 3 Al 2 o 3 TiO 2 SiO 2 content(%) 7.44 3.39 1.4558 15.82 0.082 70.58
[0029] The feldspar raw ore is ground until the iron mineral monomer is dissociated. figure 1 The feldspar ore sorting process flow shown is for sorting the ore.
[0030] The separation conditions are as follows: grind 500 grams of ore samples to -0.018mm particle size accounting for 95.5%, conduct a magnetic separation at a concentration of 60%, and the...
PUM
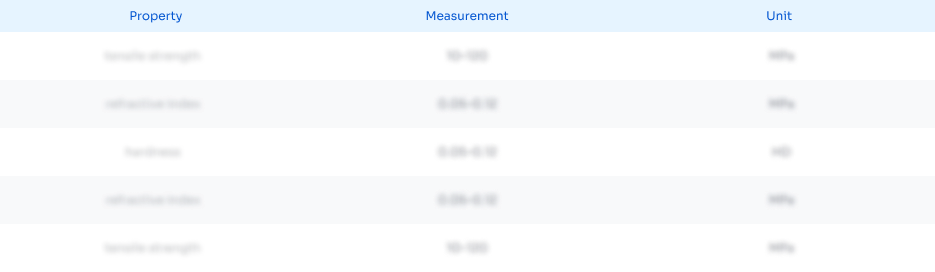
Abstract
Description
Claims
Application Information

- Generate Ideas
- Intellectual Property
- Life Sciences
- Materials
- Tech Scout
- Unparalleled Data Quality
- Higher Quality Content
- 60% Fewer Hallucinations
Browse by: Latest US Patents, China's latest patents, Technical Efficacy Thesaurus, Application Domain, Technology Topic, Popular Technical Reports.
© 2025 PatSnap. All rights reserved.Legal|Privacy policy|Modern Slavery Act Transparency Statement|Sitemap|About US| Contact US: help@patsnap.com