Preparation method and application of benzoxazine-maleamide resin mixture
A technology of resin mixture and maleamide, applied in the direction of chemical instruments and methods, synthetic resin layered products, layered products, etc., can solve the problem of high cost, difficult to obtain raw materials, unsuitable for general engineering composite materials and electrical insulation material products Manufacturing and other issues to achieve low cost, good commercial effect, and good apparent quality
- Summary
- Abstract
- Description
- Claims
- Application Information
AI Technical Summary
Problems solved by technology
Method used
Image
Examples
Embodiment 1
[0025] Put 180kg of amine compounds (aniline: ethylenediamine: 1,6 hexamethylenediamine = 4:2:1), 100kg of maleic anhydride and 420kg of toluene into reactor A, and quickly The temperature was raised to 95° C. for 2 hours to obtain an intermediate solution, which was lowered to room temperature for later use.
[0026] In reactor B, put all the intermediate solution in reactor A, after cooling down to 7℃~10℃, add 275kg of 40% formaldehyde solution, control the temperature not to exceed 20℃ for 1 hour, adjust pH=6~ 7. Add 180kg of phenol and 140kg of toluene, stir and react at a temperature of 90°C for 3.5 hours, separate into an organic phase and an aqueous phase after standing still, remove the water in the lower part of the reactor, remove the solvent by vacuum distillation, and dry to obtain Pale brown-yellow solid benzene-horse resin mixture.
Embodiment 2
[0028] Put 190kg of amine compounds (aniline: ethylenediamine = 2:1), 110kg of maleic anhydride and 430kg of toluene into reactor A. Under stirring, rapidly raise the temperature to 70°C and react for 1.5 hours to obtain The intermediate solution was lowered to room temperature for later use.
[0029] In Reactor B, put all the intermediate solution in Reactor A, and then lower the temperature to 14°C~17°C, then add 290kg of 40% formaldehyde solution, control the temperature not to exceed 20°C for 1.5 hours, and adjust the pH=6 ~7, then add 190kg of phenolic compound (phenol: cresol = 2:5) and 145kg of toluene, stir and react at a temperature of 95°C for 4 hours, separate into an organic phase and an aqueous phase after standing, and remove the lower part of the reactor water, then vacuum distillation to remove the solvent, and drying to obtain a light brown solid benzene-horse resin mixture.
Embodiment 3
[0031] Put 180kg of amine compounds (aniline: ethylenediamine: 4,4'-diaminodiphenyl ether = 5:2:1), 90kg of maleic anhydride and 440kg of toluene into reactor A. Under stirring, the temperature was raised rapidly to 85° C. for 2 hours to obtain an intermediate solution, which was lowered to room temperature for later use.
[0032] In Reactor B, put all the intermediate solutions in Reactor A, and after cooling down to 18°C-20°C, add 260kg of 40% formaldehyde in paraformaldehyde aqueous solution, control the temperature not to exceed 20°C for 2 hours, adjust pH=6~7, then add 170kg of phenolic compound (phenol:cresol=1:2) and 140kg of toluene, stir and react at 95℃ for 4 hours, separate into organic phase and water phase after standing, remove The water in the lower part of the reactor was then vacuum distilled to remove the solvent and dried to obtain a light brown solid benzene-horse resin mixture.
PUM
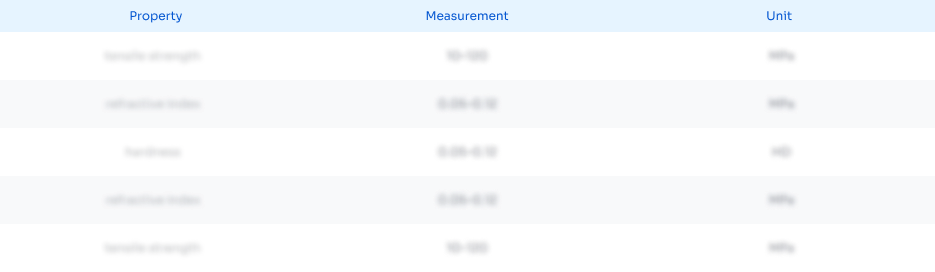
Abstract
Description
Claims
Application Information

- R&D
- Intellectual Property
- Life Sciences
- Materials
- Tech Scout
- Unparalleled Data Quality
- Higher Quality Content
- 60% Fewer Hallucinations
Browse by: Latest US Patents, China's latest patents, Technical Efficacy Thesaurus, Application Domain, Technology Topic, Popular Technical Reports.
© 2025 PatSnap. All rights reserved.Legal|Privacy policy|Modern Slavery Act Transparency Statement|Sitemap|About US| Contact US: help@patsnap.com