Manganese dioxide nanorod/graphene composite electrode material and preparation method thereof
A graphene composite and electrode material technology, which is applied in the manufacture of hybrid capacitor electrodes, hybrid/electric double layer capacitors, etc., can solve the problems of electrochemical performance impact, poor conductivity of MnO2, etc., achieve low raw material cost, easy graphene composite, highly reproducible results
- Summary
- Abstract
- Description
- Claims
- Application Information
AI Technical Summary
Problems solved by technology
Method used
Image
Examples
Embodiment 1
[0021] 1). Graphite oxide (GO) was prepared by the modified Hummers method.
[0022] 2). Disperse the prepared GO in deionized water and ultrasonically treat it for 60min to obtain a dispersion solution of GO (0.5mg mL -1 ).
[0023] 3). Add 30wt% glucose and 25wt% ammonia water to the above solution and stir for 15min. Then the mixed solution was stirred in a 95 °C water bath for 1 h.
[0024] 4). After cooling, the black uniform suspension was centrifuged, filtered and washed, and dried at 50° C. for 12 hours to obtain pure graphene. GO, glucose, and ammonia can be scaled proportionally. The specific volume ratio is GO dispersion liquid: glucose solution: ammonia water = 100:10:1.
[0025] 5). Disperse 0.05g graphene in 80mL deionized water and sonicate for 20min.
[0026] 6). The equimolar concentration of MnSO 4 and KMnO 4 (0.03M) was added to the above solution and stirred for 1 h to obtain a precursor solution. Graphene, MnSO 4 , KMnO 4 All three can be scaled ...
Embodiment 2
[0030] 1). Graphite oxide (GO) was prepared by the modified Hummers method.
[0031] 2). Disperse the prepared GO in deionized water and ultrasonically treat it for 60min to obtain a dispersion solution of GO (0.5mg mL -1 ).
[0032] 3). Add 30wt% glucose and 25wt% ammonia water to the above solution and stir for 15min. Then the mixed solution was stirred in a 95 °C water bath for 1 h.
[0033] 4). After cooling, the black uniform suspension was centrifuged, filtered and washed, and dried at 50° C. for 12 hours to obtain pure graphene. GO, glucose, and ammonia can be scaled proportionally. The specific volume ratio is GO dispersion liquid: glucose solution: ammonia water = 100:10:1.
[0034] 5). Disperse 0.05g graphene in 80mL deionized water and sonicate for 20min.
[0035] 6). The equimolar concentration of MnSO 4 and KMnO 4 (0.06M) was added to the above solution and stirred for 1 h to obtain a precursor solution. Graphene, MnSO 4 , KMnO 4 All three can be scaled ...
Embodiment 3
[0039] 1). Graphite oxide (GO) was prepared by the modified Hummers method.
[0040]2). Disperse the prepared GO in deionized water and ultrasonically treat it for 60min to obtain a dispersion solution of GO (0.5mg mL -1 ).
[0041] 3). Add 30wt% glucose and 25wt% ammonia water to the above solution and stir for 15min. Then the mixed solution was stirred in a 95 °C water bath for 1 h.
[0042] 4). After cooling, the black uniform suspension was centrifuged, filtered and washed, and dried at 50° C. for 12 hours to obtain pure graphene. GO, glucose, and ammonia can be scaled proportionally. The specific volume ratio is GO dispersion liquid: glucose solution: ammonia water = 100:10:1.
[0043] 5). Disperse 0.05g graphene in 80mL deionized water and sonicate for 20min.
[0044] 6). The equimolar concentration of MnSO 4 and KMnO 4 (0.03M) was added to the above solution and stirred for 1 h to obtain a precursor solution. Graphene, MnSO 4 , KMnO 4 All three can be scaled p...
PUM
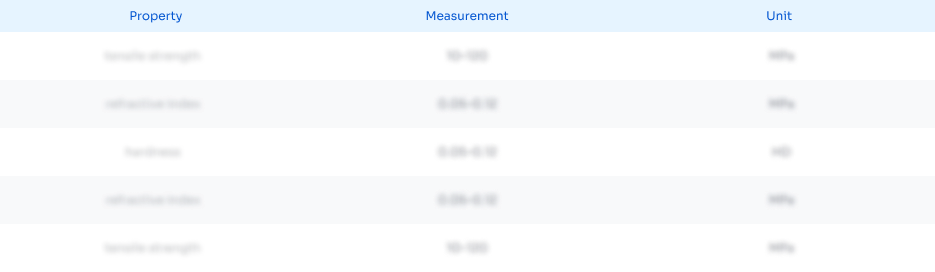
Abstract
Description
Claims
Application Information

- R&D
- Intellectual Property
- Life Sciences
- Materials
- Tech Scout
- Unparalleled Data Quality
- Higher Quality Content
- 60% Fewer Hallucinations
Browse by: Latest US Patents, China's latest patents, Technical Efficacy Thesaurus, Application Domain, Technology Topic, Popular Technical Reports.
© 2025 PatSnap. All rights reserved.Legal|Privacy policy|Modern Slavery Act Transparency Statement|Sitemap|About US| Contact US: help@patsnap.com