Preparation method of Ti5O9 nanoparticles formed in plain carbon steel
A nano-particle, ordinary carbon steel technology, applied in the field of iron and steel materials
- Summary
- Abstract
- Description
- Claims
- Application Information
AI Technical Summary
Problems solved by technology
Method used
Examples
Embodiment 1
[0022] 1) Alloy raw materials: Common carbon steel is used, C: 0.12wt.%, Mn: 0.50wt.%, Si: 0.30wt.%, S: 0.040wt.%, P: 0.035wt.%. The alloy weighs 7.8kg.
[0023] 2) Metal mold casting with internal ceramic coating is adopted, and the metal mold is heated to 200°C before pouring;
[0024] 3) In order to reduce air inhalation, heat the alloy raw material and graphite sprue cup to 200°C in a resistance furnace, keep it warm for 2 hours and dry it;
[0025] 4) Put the alloy raw material into the crucible, and install the mold on the centrifugal disc in the vacuum furnace. Then install the sprue cup bracket, sprue cup and ceramic filter. Align the nozzle of the sprue cup with the center of the gate on the mold. Close the furnace door and furnace cover, open the vacuum system to evacuate the furnace body, when the vacuum degree reaches 5×10 -1 Pa, turn off the vacuum system and fill with N 2 Gas up to 0.5MPa;
[0026] 5) The alloy is smelted by power transmission and heating. ...
Embodiment 2
[0031] 1) Alloy raw materials: Common carbon steel is used, C: 0.22wt.%, Mn: 0.50~1.4wt.%, Si≤0.35wt.%, S: 0.045wt.%, P: 0.045wt.%. The alloy weighs 7.8kg.
[0032] 2) Metal mold casting with internal ceramic coating is adopted, and the metal mold is heated to 200°C before pouring;
[0033] 3) In order to reduce air inhalation, heat the alloy raw material and graphite sprue cup to 200°C in a resistance furnace, keep it warm for 2 hours and dry it;
[0034] 4) Put the alloy raw material into the crucible, and install the mold on the centrifugal disc in the vacuum furnace. Then install the sprue cup bracket, sprue cup and ceramic filter. Align the nozzle of the sprue cup with the center of the gate on the mold. Close the furnace door and furnace cover, open the vacuum system to evacuate the furnace body, when the vacuum degree reaches 5×10 -1 Pa, turn off the vacuum system and fill with N 2 Gas up to 0.5MPa;
[0035]5) The alloy is smelted by power transmission and heating...
PUM
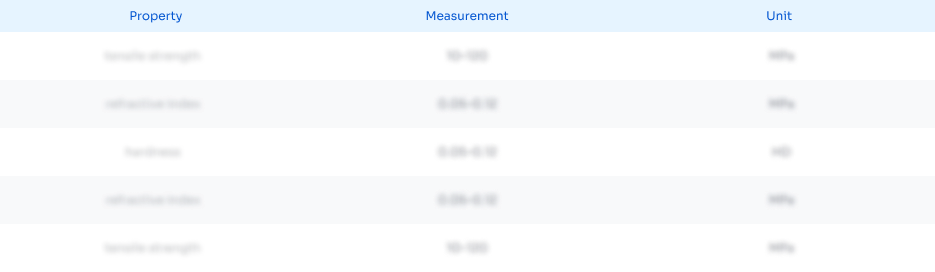
Abstract
Description
Claims
Application Information

- R&D Engineer
- R&D Manager
- IP Professional
- Industry Leading Data Capabilities
- Powerful AI technology
- Patent DNA Extraction
Browse by: Latest US Patents, China's latest patents, Technical Efficacy Thesaurus, Application Domain, Technology Topic, Popular Technical Reports.
© 2024 PatSnap. All rights reserved.Legal|Privacy policy|Modern Slavery Act Transparency Statement|Sitemap|About US| Contact US: help@patsnap.com