Method of treating waste residue in production of neopentyl glycol
A technology of neopentyl glycol and waste residues, applied in the separation/purification of hydroxyl compounds, separation/purification of carboxylic acid compounds, organic chemistry, etc., can solve the problem of low economic benefits, narrow use range of dark sodium formate residues, environmental pollution, etc. problem, to achieve the effect of high purity, easy realization and simple process
- Summary
- Abstract
- Description
- Claims
- Application Information
AI Technical Summary
Problems solved by technology
Method used
Examples
Embodiment 1
[0024] Example 1 It is determined that a certain neopentyl glycol production waste residue contains 84% of sodium formate, 6% of neopentyl glycol, and 6% of moisture, and the others are unknown impurities, and the color is brownish black. Utilize the present invention to reclaim high-purity sodium formate and neopentyl glycol method from neopentyl glycol production waste residue: the waste residue is dissolved with water to obtain the sodium formate thick solution of concentration 30%, and the solution successively passes precision filter and ultrafiltration device to remove wherein insoluble matter and The particulate impurities then enter the nanofiltration device for nanofiltration separation, the operating temperature is 40°C, and the operating pressure is 2.5MPa. The nanofiltration permeate is evaporated, concentrated and crystallized to obtain a sodium formate product with a purity of 95.9%. The product is white; the black solid impurities obtained by evaporating and co...
Embodiment 2
[0025] Example 2 It is determined that a neopentyl glycol production waste residue contains 81% sodium formate, 6% neopentyl glycol, and 8% moisture, and the others are unknown impurities, black. Utilize the present invention to reclaim high-purity sodium formate and neopentyl glycol method from neopentyl glycol production waste residue: the waste residue is dissolved with water to obtain the sodium formate rough solution of concentration 40%, and the solution successively passes precision filter and ultrafiltration device to remove wherein insoluble matter and The particulate impurities then enter the nanofiltration device for nanofiltration separation. The operating temperature is 45°C and the operating pressure is 2.3MPa. The nanofiltration permeate is evaporated, concentrated, and crystallized to obtain a sodium formate product with a purity of 95.5%, which is white crystals; the black solid impurities obtained by evaporating and concentrating the nanofiltration concentrate...
Embodiment 3
[0026] In Example 3, it was determined that a neopentyl glycol production waste residue contained 84% sodium formate, 5% neopentyl glycol, and 8% moisture, and the others were unknown impurities. Utilize the method for processing neopentyl glycol production waste residue of the present invention, the steps are as follows: (1) neopentyl glycol production waste residue is dissolved in water to obtain crude sodium formate solution, and the concentration of the crude sodium formate solution is controlled to be 10%; (2) the crude sodium formate solution is subjected to precise The filter and ultrafiltration device filter to remove particulate impurities. The molecular weight cut-off of the ultrafiltration membrane is 2000, and the ultrafiltration temperature is 20°C; (3) The solution after removing particulate impurities enters the nanofiltration system for nanofiltration separation. The molecular weight is 150, the operating temperature during nanofiltration separation is 20°C, and...
PUM
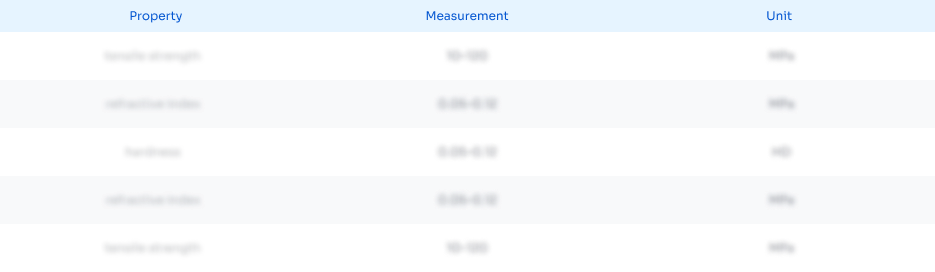
Abstract
Description
Claims
Application Information

- Generate Ideas
- Intellectual Property
- Life Sciences
- Materials
- Tech Scout
- Unparalleled Data Quality
- Higher Quality Content
- 60% Fewer Hallucinations
Browse by: Latest US Patents, China's latest patents, Technical Efficacy Thesaurus, Application Domain, Technology Topic, Popular Technical Reports.
© 2025 PatSnap. All rights reserved.Legal|Privacy policy|Modern Slavery Act Transparency Statement|Sitemap|About US| Contact US: help@patsnap.com