Wear resistance casting material for ladle
A technology of castables and ladles, applied in the field of castables, can solve problems such as short service life and poor wear resistance, and achieve the effects of good construction performance, easy slag removal, and excellent thermal shock stability
- Summary
- Abstract
- Description
- Claims
- Application Information
AI Technical Summary
Problems solved by technology
Method used
Image
Examples
Embodiment 1
[0017] A wear-resistant castable for ladle, the components and weight of the castable are: 100Kg of corundum material; 10Kg of silicon carbide; 1Kg of graphite; 0.1Kg of explosion-proof agent; 0.1Kg of composite admixture; In the corundum material, corundum aggregate is 60Kg and corundum fine powder 40Kg, silicon carbide is black silicon carbide with a content of 93%, graphite is flake graphite, the explosion-proof agent of this embodiment is fiber, and the composite admixture of this embodiment is sodium phosphate, also It can be phosphate such as potassium phosphate, and the binder in this embodiment is alumina.
Embodiment 2
[0019] A wear-resistant castable for ladle, the components and weight of the castable are: 100Kg of corundum material; 50Kg of silicon carbide; 5Kg of graphite; 0.5Kg of explosion-proof agent; 0.5Kg of composite admixture; The corundum aggregate in the corundum material is 70Kg and corundum fine powder 30Kg, the silicon carbide is black silicon carbide with a content of 95%, and the graphite is flake graphite. The explosion-proof agent in this embodiment is aluminum chloride, the composite admixture in this embodiment is sodium carboxylate, or carboxylate such as potassium carboxylate, and the bonding agent in this embodiment is silicon oxide.
Embodiment 3
[0021] A wear-resistant castable for ladle, the components and weight of the castable are: 100Kg of corundum material; 90Kg of silicon carbide; 9Kg of graphite; 0.9Kg of explosion-proof agent; 0.9Kg of composite admixture; In the corundum material, corundum aggregate is 70Kg and corundum fine powder 30Kg, silicon carbide is black silicon carbide with a content of 91%, graphite is flake graphite, the explosion-proof agent of this embodiment is aluminum chloride, and the composite admixture of this embodiment is stearin acid, the binder is zirconia.
[0022] After weighing according to the weight ratio during the production of the present invention, these raw materials are measured according to the principle of the closest packing, and after mixing, the viscous substance is formed, or has plasticity, or has certain fluidity, and can be pounded or formed by vibration. When in use, spread the mixed materials in the ladle, the bottom of the ladle need not be supported, and the side...
PUM
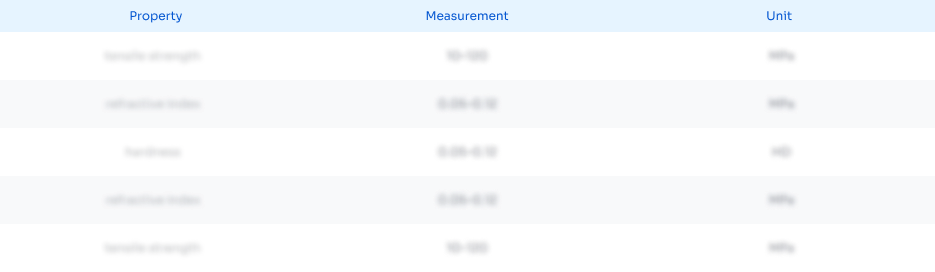
Abstract
Description
Claims
Application Information

- R&D
- Intellectual Property
- Life Sciences
- Materials
- Tech Scout
- Unparalleled Data Quality
- Higher Quality Content
- 60% Fewer Hallucinations
Browse by: Latest US Patents, China's latest patents, Technical Efficacy Thesaurus, Application Domain, Technology Topic, Popular Technical Reports.
© 2025 PatSnap. All rights reserved.Legal|Privacy policy|Modern Slavery Act Transparency Statement|Sitemap|About US| Contact US: help@patsnap.com