Integral reinforced solid wood section bar and manufacturing method thereof
A profile and integral technology, applied in the field of integrally reinforced solid wood profiles and their manufacturing, can solve the problems of uneven moisture distribution in profiles, affecting the appearance of wood, and high cost, shortening the heating and softening time, avoiding cracking and deformation defects, equipment and The effect of low personnel requirements
- Summary
- Abstract
- Description
- Claims
- Application Information
AI Technical Summary
Problems solved by technology
Method used
Image
Examples
Embodiment 1
[0033] Select Daqing poplar as the test material, and saw the same specification of the plate according to the size of the press plate. The sawn boards are stacked, and the top of the pile is weighted. Use a forklift to put the stacked wood into a steam-heated top-wind drying kiln for drying and drying, and control its moisture content at 3%. Use a four-sided planer to polish both sides of the dried profile. The resulting polished surface is parallel to the fiber direction of the wood. Put the resulting polished log with a thickness of 25 mm into a three-layer hot press. Adjust the temperature of the press platen to 180 ° C. The pressing speed of the pressing plates is 3mm / s. When the upper and lower pressing plates are just in contact with the wood surface, the heat is kept for 400s, and the wood is heated and softened. After softening, close the press and compress the wood in the hot press to 19mm. The pressure of the hot press is 10MPa (equivalent to 103.32kg / cm 2 ), press...
Embodiment 2
[0037] Select Poplar tomentosa wood, and saw the board with the same specification according to the size of the press board. The sawn boards are stacked, and the top of the pile is weighted, and the stacked wood is dried and dried in a steam-heated top-wind drying kiln with a forklift, and the moisture content is controlled at 2%. Use a four-sided planer to polish both sides of the dried profile. The resulting polished surface is parallel to the fiber direction of the wood. Put the obtained polished log with a thickness of 27mm into a three-layer hot press. Adjust the temperature of the press platen to 190°C. The pressing speed of the pressing plates is 3mm / s. When the upper and lower pressing plates are just in contact with the surface of the log, the heat is kept for 350s, and the wood is heated and softened. After softening, close the press and compress the wood in the hot press to 19mm. When pressing, the pressure of the hot press is 12MPa (equivalent to 123.984kg / cm 2 ),...
Embodiment 3
[0041] Select paulownia wood, and perform sawing of the same specification on the board according to the size of the press board. The sawn boards are stacked, and the top of the pile is weighted. Use a forklift to put the stacked wood into a steam-heated top-wind drying kiln for drying and drying, and control its moisture content at 3%. Use a four-sided planer to polish both sides of the dried profile. The resulting polished surface is parallel to the fiber direction of the wood. Put the polished log with a thickness of 25mm into a three-layer hot press. Adjust the temperature of the press platen to 190°C. The pressing speed of the pressing plates is 3mm / s. When the upper and lower pressing plates are just in contact with the wood surface, the heat is kept for 450s, and the wood is heated and softened. After softening, close the press and compress the wood in the hot press to 19mm. When pressing, the pressure of the hot press is 8MPa (equivalent to 82.656kg / cm 2 ), keep the p...
PUM
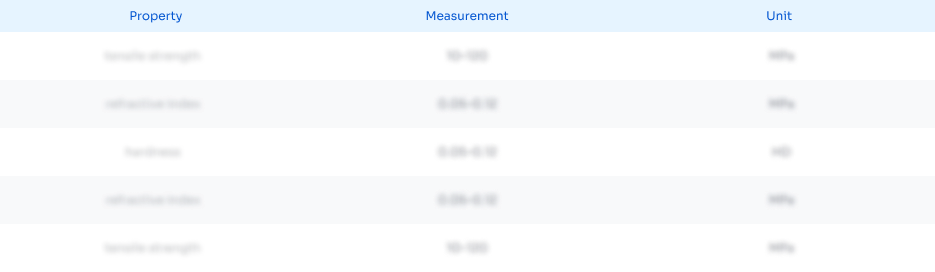
Abstract
Description
Claims
Application Information

- R&D
- Intellectual Property
- Life Sciences
- Materials
- Tech Scout
- Unparalleled Data Quality
- Higher Quality Content
- 60% Fewer Hallucinations
Browse by: Latest US Patents, China's latest patents, Technical Efficacy Thesaurus, Application Domain, Technology Topic, Popular Technical Reports.
© 2025 PatSnap. All rights reserved.Legal|Privacy policy|Modern Slavery Act Transparency Statement|Sitemap|About US| Contact US: help@patsnap.com