Coating machine for coating silicon-steel magnesium oxide coating liquid
A magnesium oxide and coating machine technology, which is applied to the device and coating of the surface coating liquid, can solve the problems of affecting the coating quality, coating liquid accumulation and scaling, and agglomeration deposition, so as to improve the continuous production efficiency , Continuous production stability, and the effect of reducing operating intensity
- Summary
- Abstract
- Description
- Claims
- Application Information
AI Technical Summary
Problems solved by technology
Method used
Image
Examples
Embodiment 1
[0044] refer to Figure 1~Figure 3 As shown, the coating machine for silicon steel magnesia coating solution described in this embodiment includes a frame, an upper coating roller 1, a lower coating roller 2, a magnesia coating solution circulation device 3, and a spray pipe 5 , the upper coating roller 1 and the lower coating roller 2 are all installed on the frame, and the spray pipe 5 is connected with the magnesium oxide coating liquid circulation device 3, and is used for the magnesium oxide coating liquid in the magnesium oxide coating liquid circulation device 3 It is sprayed onto the upper surface of the steel strip 4, and also includes a coating liquid diverter 6 and a baffle plate 7. The coating liquid diverter 6 is arranged on one side of the lower coating roller 2 and is installed on the frame. The coating liquid diverter 6 includes at least one bottom plate 9, the edge of the bottom plate 9 facing the side of the lower coating roller 2 is the drainage edge 10, and...
Embodiment 2
[0049] Such as Figure 4 and Figure 5 As shown, the present embodiment is roughly the same as Embodiment 1, except that the two sides of the side plate 12 connected to the collecting edge 11 opposite to the draining edge 10 on the bottom plate 9 of the coating liquid diverter 6 are arc-shaped, and the side The angle formed by the plate 12 and the bottom plate 9 is an obtuse angle.
Embodiment 3
[0051] Such as Figure 6 and Figure 7 As shown, the present embodiment is roughly the same as Embodiment 1, except that the two collecting edges 11 connected to the draining edge 10 on the bottom plate 9 of the coating liquid diverter 6 are arc-shaped, and are provided with side plates 12; the bottom plate The collecting side 11 opposite to the draining side 10 on 9 is not connected to the side plate;
PUM
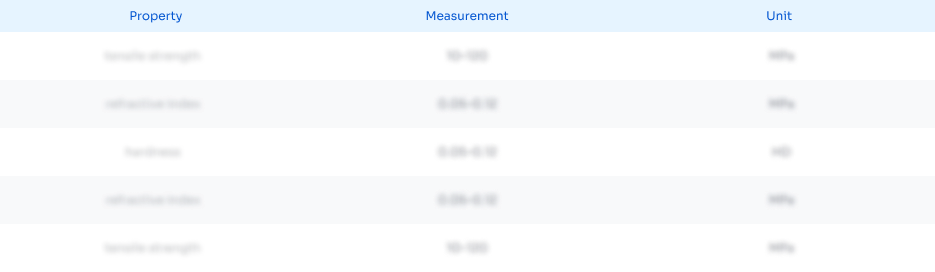
Abstract
Description
Claims
Application Information

- R&D Engineer
- R&D Manager
- IP Professional
- Industry Leading Data Capabilities
- Powerful AI technology
- Patent DNA Extraction
Browse by: Latest US Patents, China's latest patents, Technical Efficacy Thesaurus, Application Domain, Technology Topic, Popular Technical Reports.
© 2024 PatSnap. All rights reserved.Legal|Privacy policy|Modern Slavery Act Transparency Statement|Sitemap|About US| Contact US: help@patsnap.com