Energy-saving method for preparing yellow phosphorus from low-quality phosphate ore
A phosphate rock, low-quality technology, applied in chemical instruments and methods, phosphorus compounds, inorganic chemistry, etc., can solve problems such as high requirements for refractory materials in tunnel kilns, failure to meet energy saving and emission reduction, and affect normal production, etc., to achieve fast and efficient Utilize heat energy, save thorough drying time, and have the effect of no dust leakage
- Summary
- Abstract
- Description
- Claims
- Application Information
AI Technical Summary
Problems solved by technology
Method used
Image
Examples
Embodiment 1
[0031] with P 2 o 5 24.59%, CaO 43.61%, SiO 2 9.7%, CO 2 10.86% phosphate rock is used as the raw ore. After the raw ore is pretreated, it is different from the existing technology. It is first dried and then pelletized to obtain a content of P 2 o 5 29.80%, CaO 42.24%,, SiO 2 14.12%, CO 2 <0.5% phosphate rock, and finally use the electric furnace reduction production method to obtain yellow phosphorus.
[0032] Choosing low-quality phosphate rock as the raw material for yellow phosphorus production avoids the mining mode of "mining the rich and abandoning the poor" adopted by most small and medium-sized enterprises today, thereby rationally utilizing mineral resources and avoiding a large amount of waste of phosphate rock resources.
[0033] In addition, the existing methods for preparing yellow phosphorus all use the method of first forming into balls and then drying and then reducing. Since the spheres will be firmly squeezed during the process of forming into ba...
Embodiment 2
[0040] Similar to Example 1, the ball forming process is placed after the drying process. The difference is that in Example 2, flash drying is used in the drying process, specifically:
[0041] with P 2 o 5 24.59%, CaO 43.61%, SiO 2 9.7%, CO 210.86% phosphate rock is used as the raw ore. After the raw ore is pulverized and pretreated, the wet phosphate rock powder is obtained. The wet phosphate rock powder is sent into the dryer with a screw feeder, and the heat generated by calcination is used for heat exchange. After absorbing the cold fluid of the device, it is used as a drying heat source - hot air. The hot air flash-dries the wet phosphate rock powder at an inlet temperature of 300-350°C or 350-400°C at a speed of 5-9m / s to obtain a dry phosphate rock powder. At this time, the outlet temperature at the outlet of the dryer is 50≤T<100°C. After collecting the dry phosphate rock powder with a cyclone separator and preheating it, put it into the calciner, and the calcine...
Embodiment 3
[0046] Similar to the steps of Example 2, different from Example 2, the calcination process has adopted a dynamic calcination process, specifically:
[0047] with P 2 o 5 24.59%, CaO 43.61%, SiO 2 9.7%, CO 2 10.86% phosphate rock is used as the raw ore. After the raw ore is washed and pretreated, the wet phosphate rock powder is obtained. The wet phosphate rock powder is sent into the dryer with a screw feeder, and the heat of the exhaust gas generated by calcination is used for heat exchange. After absorbing the cold fluid of the device, it is used as a drying heat source - hot air, and the hot air is used at a speed of 10-15m / s to flash-dry the phosphate rock powder at an inlet temperature of 400-450°C or 450-500°C to obtain a dry phosphate rock powder. The outlet temperature at the outlet of the dryer is 100≤T<150°C. The dry phosphate rock powder is collected by a cyclone separator and preheated, and then put into the calciner. During calcination, the dry phosphate ro...
PUM
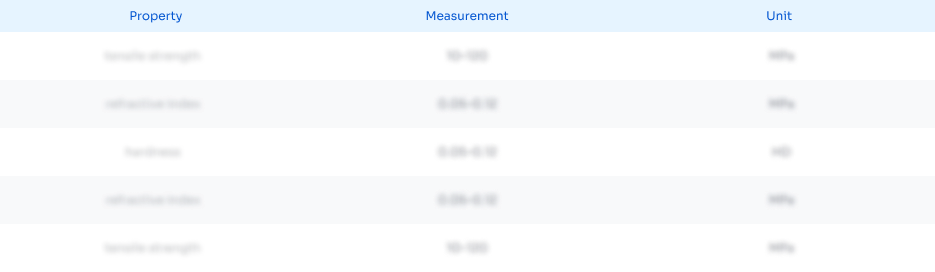
Abstract
Description
Claims
Application Information

- R&D
- Intellectual Property
- Life Sciences
- Materials
- Tech Scout
- Unparalleled Data Quality
- Higher Quality Content
- 60% Fewer Hallucinations
Browse by: Latest US Patents, China's latest patents, Technical Efficacy Thesaurus, Application Domain, Technology Topic, Popular Technical Reports.
© 2025 PatSnap. All rights reserved.Legal|Privacy policy|Modern Slavery Act Transparency Statement|Sitemap|About US| Contact US: help@patsnap.com