A method for separating rare earth resources in rare earth slag by supergravity
A super-gravity, rare earth technology, applied in the field of efficient separation and utilization of symbiotic resources, can solve the problems of large dosage of chemicals, high grinding cost, low recovery rate of rare earth resources, etc., to improve the yield and quality, realize comprehensive utilization, solve Effects of Environmental Load Problems
- Summary
- Abstract
- Description
- Claims
- Application Information
AI Technical Summary
Problems solved by technology
Method used
Image
Examples
Embodiment 1
[0039] Take 10kg of 1# Baotou Steel blast furnace rich rare earth slag, grind it to below 200 mesh, after testing, its binary alkalinity CaO / SiO 2 1.28, CaF 2 The content is 13% of the rare earth slag, so add 0.5kg CaO and CaF to the slag 2 Mixed materials with a mass ratio of 1:1 to adjust the alkalinity to 1.7, CaF 2 The content reaches 16% of the rare earth slag. After mixing, heat it to 1400°C and keep it for 30 minutes to ensure that the ingredients are mixed evenly, then quickly cool to 1300°C, and then use the cooling rate of 0.5°C / min to promote the rare earth slag in the temperature range of 1300-1150°C. The rare earth elements are enriched in the ceria fluorosilica phase, and finally precipitate and grow in the form of ceria fluorosilica crystals. After the slag heat treatment is completed, adjust the slag temperature to 1200°C and immediately start the centrifuge with a built-in ceramic feeding inner spiral lining, adjust the speed of the centrifuge so that the gr...
Embodiment 2
[0042] Take 10kg of 1# Baotou Steel blast furnace rich rare earth slag, grind it to below 200 mesh, after testing, its binary alkalinity CaO / SiO 2 1.28, CaF 2 The content is 13% of the rare earth slag, so add 0.5kg CaO and CaF to the slag 2 Mixed materials with a mass ratio of 1:1 to adjust the alkalinity to 1.7, CaF 2 The content reaches 16% of the rare earth slag. After mixing, heat it to 1400°C and keep it for 30 minutes to ensure that the ingredients are mixed evenly, then quickly cool to 1300°C, and then use the cooling rate of 0.5°C / min to promote the rare earth slag in the temperature range of 1300-1150°C. The rare earth elements are enriched in the ceria fluorosilica phase, and finally precipitate and grow in the form of ceria fluorosilica crystals. After the heat treatment of the slag is completed, adjust the slag temperature to 1200°C and immediately start the centrifuge with a built-in ceramic feeding inner spiral lining, adjust the speed of the centrifuge so that...
Embodiment 3
[0044] Take 10kg of 1# Baotou Steel blast furnace rich rare earth slag, grind it to below 200 mesh, after testing, its binary alkalinity CaO / SiO 2 1.28, CaF 2 The content is 13% of the rare earth slag, so add 0.5kg CaO and CaF to the slag 2 Mixed materials with a mass ratio of 1:1 to adjust the alkalinity to 1.7, CaF 2 The content reaches 16% of the rare earth slag. After mixing, heat it to 1400°C and keep it for 30 minutes to ensure that the ingredients are mixed evenly, then quickly cool to 1300°C, and then use the cooling rate of 0.5°C / min to promote the rare earth slag in the temperature range of 1300-1150°C. The rare earth elements are enriched in the ceria fluorosilica phase, and finally precipitate and grow in the form of ceria fluorosilica crystals. After the heat treatment of the slag is completed, adjust the temperature of the slag to 1200°C and immediately start the centrifuge with a built-in porous ceramic filter, adjust the speed of the centrifuge so that the gr...
PUM
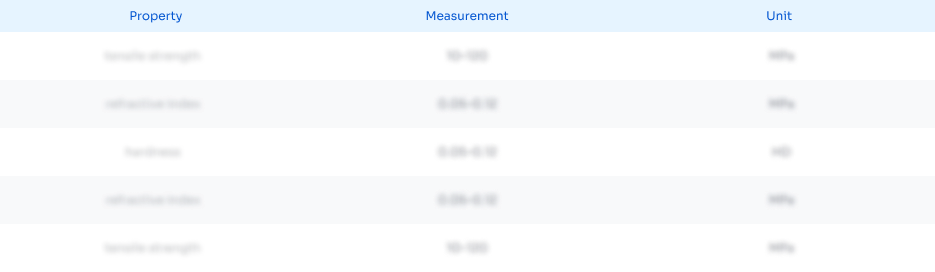
Abstract
Description
Claims
Application Information

- R&D
- Intellectual Property
- Life Sciences
- Materials
- Tech Scout
- Unparalleled Data Quality
- Higher Quality Content
- 60% Fewer Hallucinations
Browse by: Latest US Patents, China's latest patents, Technical Efficacy Thesaurus, Application Domain, Technology Topic, Popular Technical Reports.
© 2025 PatSnap. All rights reserved.Legal|Privacy policy|Modern Slavery Act Transparency Statement|Sitemap|About US| Contact US: help@patsnap.com