Modified polypropylene composite material and application thereof
A composite material and polypropylene technology, applied in the field of modified polypropylene composite materials, can solve the problems of poor solvent resistance, poor fatigue resistance, and notch sensitivity of polycarbonate, and achieve low price, high performance and price ratio, and excellent processing performance. Effect
- Summary
- Abstract
- Description
- Claims
- Application Information
AI Technical Summary
Problems solved by technology
Method used
Examples
Embodiment 1
[0032] 68.2 parts of copolymerized polypropylene, 12 parts of flame retardant decabromodiphenylethane, 3 parts of antimony trioxide, 1 part of maleic anhydride grafted polypropylene, 0.1 part of antioxidant 1010, 0.2 part of antioxidant 168, Add 0.2 parts of lubricant amide wax and 0.3 parts of coupling agent KH-550 into a high-speed mixer for high-speed mixing for 5 minutes, then transfer to a twin-screw extruder, and simultaneously extrude 15 parts of continuous alkali-free glass fiber from the twin-screw The fiber-adding port in the middle of the machine is introduced, and the material is melted and extruded at a temperature of 180-210 ° C. After being water-cooled and dried, it enters the pelletizer and pelletizes to obtain a modified polypropylene composite material. The relevant properties are shown in Table 1. The modified polypropylene composite material can be used as an electrical panel.
Embodiment 2
[0034] 62.5 parts of homopolypropylene, 12 parts of flame retardant decabromodiphenylethane, 4 parts of antimony trioxide, 10 parts of polyolefin elastomer POE, 1 part of maleic anhydride grafted polypropylene, 0.1 part of antioxidant 1010, 0.2 parts of antioxidant 168, and 0.2 parts of coupling agent KH-550 were added to a high-speed mixer for high-speed mixing for 6 minutes, and then transferred to a twin-screw extruder. At the same time, 10 parts of continuous non-alkali glass fiber from double The fiberizing port in the middle of the screw extruder is introduced, and the material is melted and extruded at a temperature of 180~210°C, and then enters a pelletizer to pelletize after being water-cooled and dried to obtain a modified polypropylene composite material. The relevant properties are shown in Table 1 . The modified polypropylene composite material can be used as an electrical panel.
Embodiment 3
[0036] 57.3 parts of copolymerized polypropylene, 12 parts of flame retardant decabromodiphenylethane, 4 parts of antimony trioxide, 15 parts of polyolefin elastomer POE, 1 part of maleic anhydride grafted polypropylene, 0.1 part of antioxidant 1010 , 0.2 part of antioxidant 168, 0.2 part of lubricant polypropylene wax, 0.2 part of coupling agent KH-550, join in the high-speed mixer and carry out high-speed mixing for 5 minutes, then transfer to the twin-screw extruder, at the same time, 10 parts The continuous non-alkali glass fiber is introduced from the fiberizing port in the middle of the twin-screw extruder, and the material is melted and extruded at a temperature of 180~220°C, then water-cooled and dried, and then enters the pelletizer to pelletize to obtain a modified polypropylene composite material , and its related properties are shown in Table 1. The modified polypropylene composite material can be used as an electrical panel.
[0037] Table 1
[0038]
PUM
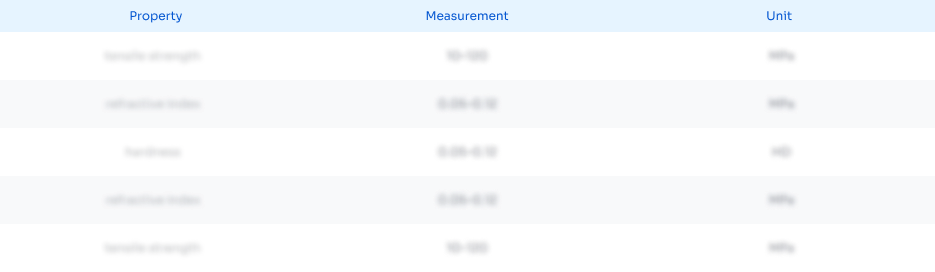
Abstract
Description
Claims
Application Information

- R&D
- Intellectual Property
- Life Sciences
- Materials
- Tech Scout
- Unparalleled Data Quality
- Higher Quality Content
- 60% Fewer Hallucinations
Browse by: Latest US Patents, China's latest patents, Technical Efficacy Thesaurus, Application Domain, Technology Topic, Popular Technical Reports.
© 2025 PatSnap. All rights reserved.Legal|Privacy policy|Modern Slavery Act Transparency Statement|Sitemap|About US| Contact US: help@patsnap.com