Manufacturing process of projection type capacitive touch screen
A technology of capacitive touch screen and manufacturing process, which is applied in the direction of electric digital data processing, instrument, data processing input/output process, etc., can solve the problems of high yield, low cost of large-size sensing film, etc., to reduce waste, The effect of reducing the process
- Summary
- Abstract
- Description
- Claims
- Application Information
AI Technical Summary
Problems solved by technology
Method used
Image
Examples
Embodiment Construction
[0030] The present invention will be further described below in conjunction with accompanying drawing.
[0031] Such as figure 1 Shown, concrete steps of the present invention are:
[0032] Step 1, place the clean scratch-resistant PET base material on the 3D printing platform 4 with the scratch-resistant surface facing down. Called PET_X film 2. Place the PET base material with adhesive layer and release film protective layer on the 3D printing platform, with the release film facing down, which is called PET_Y film 3. The PET_X film and PET_Y film are precisely positioned and placed on the 3D printing platform by the robotic arm, see figure 2 .
[0033] Step 2: The robotic arm sticks the flexible flick circuit board on the PET_X film, with glue on the back of the flexible flick circuit board, and the conductive gold finger facing up. Entering the electrostatic adsorption equipment, the equipment will distribute the static electricity evenly on the two membranes.
[003...
PUM
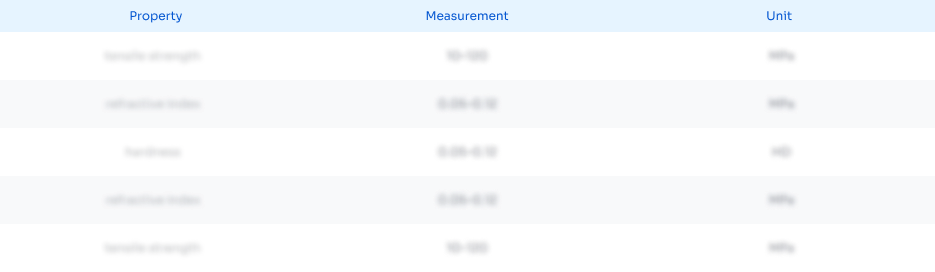
Abstract
Description
Claims
Application Information

- R&D
- Intellectual Property
- Life Sciences
- Materials
- Tech Scout
- Unparalleled Data Quality
- Higher Quality Content
- 60% Fewer Hallucinations
Browse by: Latest US Patents, China's latest patents, Technical Efficacy Thesaurus, Application Domain, Technology Topic, Popular Technical Reports.
© 2025 PatSnap. All rights reserved.Legal|Privacy policy|Modern Slavery Act Transparency Statement|Sitemap|About US| Contact US: help@patsnap.com