Heat-conducting electric insulation silicon rubber thermal interface material and preparation method thereof
A thermal interface material, silicone rubber technology, applied in the field of rubber nanocomposite materials, can solve the problem of low thermal conductivity and achieve the effect of improving thermal conductivity
- Summary
- Abstract
- Description
- Claims
- Application Information
AI Technical Summary
Problems solved by technology
Method used
Image
Examples
Embodiment 1
[0036] Sodium lauryl sulfate is added to toluene to prepare a 20mg / ml solution, and then 1 part of graphene powder is added to the solution, wherein the graphene powder mass (g) is related to the volume of the surfactant toluene solution (ml ) with a ratio of 1:500, and then ultrasonically oscillated by a 900W ultrasonic cell breaker for 60 minutes to infiltrate the graphene surface with the active agent, and finally peel the graphene into a thinner sheet structure and uniformly disperse it to obtain graphite Graphene dispersion; 200 parts of spherical thermally conductive alumina fillers were added to the graphene dispersion, and stirred evenly to make a thermally conductive filler slurry for use. Dissolve 100 parts of raw liquid silicone rubber with a viscosity of 200000cs in n-hexane, mix it with the thermally conductive filler slurry, dry the mixed mixture at 100°C, and divide it into two parts of equal mass, A component and B component. Add 3 parts of hydrogen-containing ...
Embodiment 2
[0038]Sodium lauryl sulfate is added in toluene to prepare a 20mg / ml solution, and then 2 parts of graphene powder are added to the solution, wherein the graphene powder mass (g) is related to the volume of surfactant toluene solution (ml ) with a ratio of 1:500, and then ultrasonically oscillated by a 900W ultrasonic cell breaker for 60 minutes to infiltrate the graphene surface with the active agent, and finally peel the graphene into a thinner sheet structure and uniformly disperse it to obtain graphite Graphene dispersion; 200 parts of spherical thermally conductive alumina fillers were added to the graphene dispersion, and stirred evenly to make a thermally conductive filler slurry for use. Dissolve 100 parts of raw liquid silicone rubber with a viscosity of 200000cs in n-hexane, mix it with the thermally conductive filler slurry, dry the mixed mixture at 100°C, and divide it into two parts of equal mass, A component and B component. Add 3 parts of hydrogen-containing sil...
Embodiment 3
[0040] Sodium lauryl sulfate is added to toluene to prepare a 20mg / ml solution, and then 1 part of graphene powder is added to the solution, wherein the graphene powder mass (g) is related to the volume of the surfactant toluene solution (ml ) with a ratio of 1:500, and then ultrasonically oscillated by a 900W ultrasonic cell breaker for 60 minutes to infiltrate the graphene surface with the active agent, and finally peel the graphene into a thinner sheet structure and uniformly disperse it to obtain Graphene dispersion: 300 parts of spherical heat-conducting alumina fillers are added to the graphene dispersion, stirred evenly to make a heat-conducting filler slurry, and set aside. Dissolve 100 parts of raw liquid silicone rubber with a viscosity of 200000cs in n-hexane, mix it with the thermally conductive filler slurry, dry the mixed mixture at 100°C, and divide it into two parts of equal mass, A component and B component. Add 3 parts of hydrogen-containing silicone oil cros...
PUM
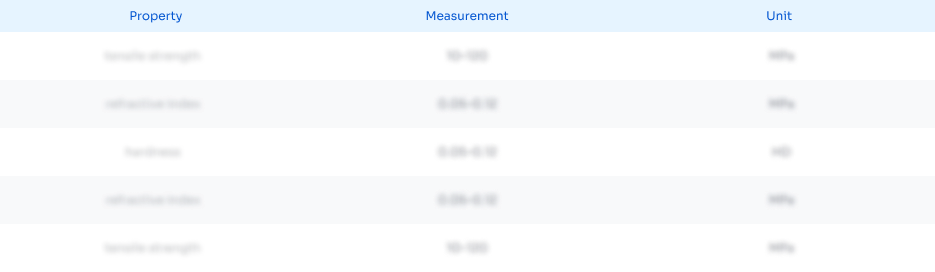
Abstract
Description
Claims
Application Information

- R&D
- Intellectual Property
- Life Sciences
- Materials
- Tech Scout
- Unparalleled Data Quality
- Higher Quality Content
- 60% Fewer Hallucinations
Browse by: Latest US Patents, China's latest patents, Technical Efficacy Thesaurus, Application Domain, Technology Topic, Popular Technical Reports.
© 2025 PatSnap. All rights reserved.Legal|Privacy policy|Modern Slavery Act Transparency Statement|Sitemap|About US| Contact US: help@patsnap.com