Method for preparing odorless and transparent 107 glue at ordinary pressure
A normal pressure and reaction technology, which is applied in the field of producing odorless and transparent 107 glue, can solve the problems of unpleasant fishy smell, yellowing of the colloid, and difficult to remove, so as to achieve no fishy smell, easy operation, and improved The effect of safety factor
- Summary
- Abstract
- Description
- Claims
- Application Information
AI Technical Summary
Problems solved by technology
Method used
Image
Examples
Embodiment 1
[0021] Pump 1000kg of the qualified raw material D4 into the dehydration kettle, heat the material to reach 50°C, blow dry nitrogen gas into it, the nitrogen flow rate is 50L / min, stir and dehydrate under 1.5KPa vacuum for 60 minutes, and then enter the polymerization reactor , add 0.02kg KOH under stirring, heat the material to 140°C, react for 90 minutes, wait until the polymerization system becomes viscous, and the molar mass of polysiloxane reaches 10 5 Above, under normal pressure, dropwise add 0.04kg H to the reactant 3 PO 4 10kg of deionized water, added dropwise while reflux, reflux degradation reaction at 160°C for 1 hour after dropwise addition, and then remove low boilers in vacuum at 170°C, separate the low boilers from deionized water and then mix with raw materials Mixing and recycling, while the finished 107 glue with low boiling matter removed is discharged into barrels through a twin-screw glue extruder. During the production process, there is no peculia...
Embodiment 2
[0023] Pump 1000kg of the qualified raw material DMC into the dehydration kettle, heat the material to reach 40°C, blow dry nitrogen gas into it, the nitrogen flow rate is 50L / min, stir and dehydrate under 1.4KPa vacuum for 80 minutes, and then enter the polymerization reaction kettle , add 0.05kg KOH under stirring, heat the material to 130°C, and react for 80 minutes, until the polymerization system becomes viscous, and the molar mass of polysiloxane reaches 10 5 Above, under normal pressure, dropwise add 0.1kg H to the reactant 3 PO 4 30kg of deionized water, added dropwise while reflux, reflux degradation reaction at 155°C for 2 hours after the dropwise addition, and then remove low boilers in vacuum at 170°C, separate the low boilers from deionized water and then mix with raw materials Mixing and recycling, while the finished 107 glue with low boiling matter removed is discharged into barrels through a twin-screw glue extruder. During the production process, there i...
Embodiment 3
[0025] Pump 1000kg of the qualified raw material D4 or DMC into the dehydration kettle, heat the material to reach 45°C, blow dry nitrogen gas into it, the nitrogen flow rate is 50L / min, stir and dehydrate under 1.3KPa vacuum for 60 minutes, and then enter the polymerization reaction kettle, add 0.035kg KOH under stirring, heat the material to 120°C, react for 60 minutes, wait until the polymerization system becomes viscous, and the molar mass of polysiloxane reaches 10 5 Above, under normal pressure, dropwise add 0.07kg H to the reactant 3 PO 4 20kg of deionized water, added dropwise while reflux, reflux degradation reaction at 150°C for 1 hour after the dropwise addition, and then remove low boilers in vacuum at 170°C, separate the low boilers from deionized water and then mix with raw materials Mixing and recycling, while the finished 107 glue with low boiling matter removed is discharged into barrels through a twin-screw glue extruder. During the production process, ther...
PUM
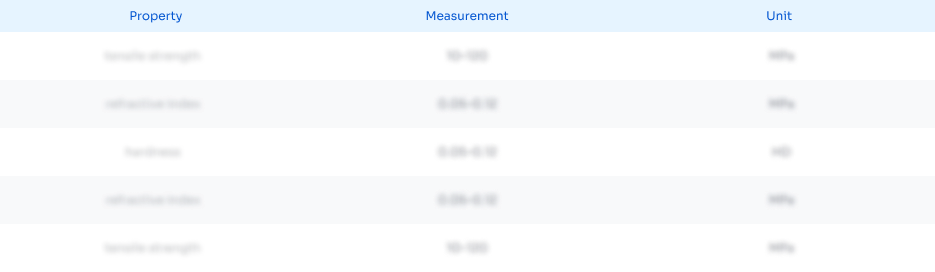
Abstract
Description
Claims
Application Information

- R&D Engineer
- R&D Manager
- IP Professional
- Industry Leading Data Capabilities
- Powerful AI technology
- Patent DNA Extraction
Browse by: Latest US Patents, China's latest patents, Technical Efficacy Thesaurus, Application Domain, Technology Topic, Popular Technical Reports.
© 2024 PatSnap. All rights reserved.Legal|Privacy policy|Modern Slavery Act Transparency Statement|Sitemap|About US| Contact US: help@patsnap.com