Method for producing potassium chloride by using blast furnace dust of iron and steel enterprises
A blast furnace gas ash and potassium chloride technology, which is applied in the direction of alkali metal chloride and the like, can solve the problems of fluctuation of blast furnace conditions, decrease of collection and dust removal efficiency of sintering head electrostatic precipitator, and increase of sintered dust particle resistance, etc. The effect of reducing the harm to the environment
- Summary
- Abstract
- Description
- Claims
- Application Information
AI Technical Summary
Problems solved by technology
Method used
Image
Examples
Embodiment 1
[0041] see figure 1 , 2, the method utilizing blast furnace gas ash of the present invention to produce potassium chloride, operation is as follows:
[0042] I) Mix gas ash and tap water at a ratio of 1:1, and perform pre-leaching for 0.5 hours. Then, the mixed solution in the pre-leaching process is sent to the leaching process, and the stirring and leaching is carried out at normal temperature, and the stirring and leaching time is 1 hour.
[0043] II) After the stirring time is reached, the mixed solution is sent to the primary filtration process for filtration, the primary filtrate is sent to the precipitation process for precipitation and impurity removal, and the primary filter residue is sent to the secondary leaching process for secondary leaching.
[0044] III) In the secondary leaching process, perform secondary leaching of the primary filter residue according to the solid-to-liquid ratio of 1:1, the leaching time is 1 hour, and then sen...
Embodiment 2
[0048] see figure 1 , 2, the method utilizing blast furnace gas ash of the present invention to produce potassium chloride, operation is as follows:
[0049] I) Mix gas ash and tap water at a ratio of 1:3, and pre-soak for 1 hour. Then the mixed solution in the pre-leaching process is sent to the leaching process, and the stirring and leaching is carried out at normal temperature, and the stirring and leaching time is 2 hours.
[0050] II) After the stirring time is reached, the mixed solution is sent to the primary filtration process for filtration, the primary filtrate is sent to the precipitation process for precipitation and impurity removal, and the primary filter residue is sent to the secondary leaching process for secondary leaching.
[0051] III) In the secondary leaching process, the primary filter residue is subjected to secondary leaching according to the solid-to-liquid ratio of 3:1. The leaching time is 2 hours, and then the mixed so...
PUM
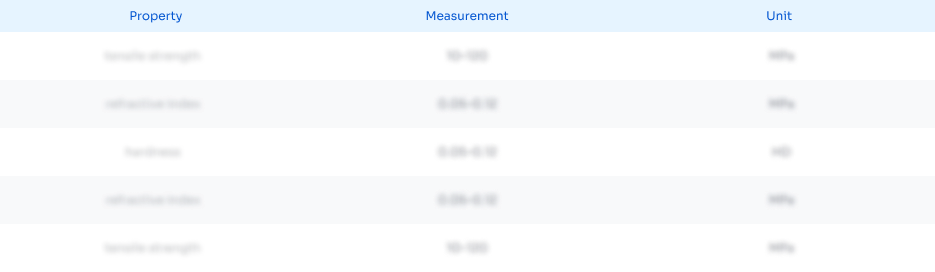
Abstract
Description
Claims
Application Information

- R&D
- Intellectual Property
- Life Sciences
- Materials
- Tech Scout
- Unparalleled Data Quality
- Higher Quality Content
- 60% Fewer Hallucinations
Browse by: Latest US Patents, China's latest patents, Technical Efficacy Thesaurus, Application Domain, Technology Topic, Popular Technical Reports.
© 2025 PatSnap. All rights reserved.Legal|Privacy policy|Modern Slavery Act Transparency Statement|Sitemap|About US| Contact US: help@patsnap.com