Forming method for conductive jack of ceramic heat dissipation substrate
A technology for heat dissipation substrates and substrates, which is applied in the reinforcement of conductive patterns, the formation of electrical connections of printed components, and the secondary treatment of printed circuits. It can solve problems such as inability to penetrate the electroplating solution, trouble employees, and increase the burden on the substrate to achieve ideal heat conduction. efficiency effect
- Summary
- Abstract
- Description
- Claims
- Application Information
AI Technical Summary
Problems solved by technology
Method used
Image
Examples
Embodiment Construction
[0048] The method for forming the conductive socket of the ceramic heat dissipation substrate of the present invention can be divided into two implementation modes with and without wires. The method of forming a conductive hole of a ceramic heat dissipation substrate without a wire is as follows: figure 1 with figure 2 Shown, including:
[0049] Substrate preparation step 100: select an alumina substrate or an aluminum nitride substrate as the main substrate 1, and form several cutting channels 11 on the surface of the substrate 1 (such as Figure 3A (Shown); the cutting lane 11 can be formed in the vertical direction, can also be formed in the lateral direction, so that the substrate can be broken from the cutting lane 11 to obtain a fixed size ceramic heat dissipation substrate unit;
[0050] Drilling step 200: Use laser drilling technology to drill a predetermined conductive hole position on the substrate 1 to form a hole 21 (such as Figure 3B Shown). Because the laser drillin...
PUM
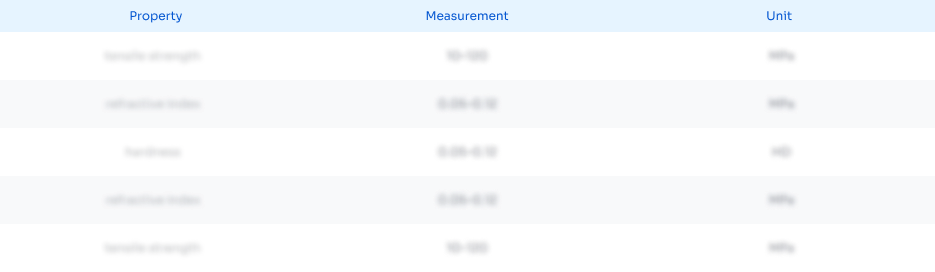
Abstract
Description
Claims
Application Information

- R&D
- Intellectual Property
- Life Sciences
- Materials
- Tech Scout
- Unparalleled Data Quality
- Higher Quality Content
- 60% Fewer Hallucinations
Browse by: Latest US Patents, China's latest patents, Technical Efficacy Thesaurus, Application Domain, Technology Topic, Popular Technical Reports.
© 2025 PatSnap. All rights reserved.Legal|Privacy policy|Modern Slavery Act Transparency Statement|Sitemap|About US| Contact US: help@patsnap.com