Square workpiece compound fixture of milling machine
A workpiece and square technology, applied in the field of compound fixtures for square workpieces, can solve the problems of low processing stability on the side of the workpiece, long auxiliary time for parts processing, low versatility of special fixtures, etc., and achieves obvious clamping effect and easy clamping force. Controlled, Simple-Structured Effects
- Summary
- Abstract
- Description
- Claims
- Application Information
AI Technical Summary
Problems solved by technology
Method used
Image
Examples
Embodiment 1
[0022] Such as figure 1 , figure 2 , image 3 As shown, the milling machine square workpiece composite fixture includes fixture seat, slide rail 1, large adjusting screw 2, moving block 3, large clamping block 4, small adjusting screw 5, fixed block 6, small clamping block 7, large clamping surface 8. Small clamping surface 9, the lower end of the slide rail 1 is installed on the fixture seat, the upper end of the slide rail 1 is stuck on the concave edge of the lower end of the moving block 3, and the large adjusting screw 2 is engaged with the moving block 3 , the lower end of the large clamping block 4 is pressed on the concave edge of the upper end of the moving block 3, the upper end of the large clamping block 4 is provided with a groove, the vertical section of the upper part of the groove is rectangular, and the lower part of the groove is a dovetail groove, The fixed block 6 is fixed on the side end of the groove of the large clamping block 4, the upper end of the ...
Embodiment 2
[0025] Such as figure 1 , figure 2 , image 3 As shown, the milling machine square workpiece composite fixture includes fixture seat, slide rail 1, large adjusting screw 2, moving block 3, large clamping block 4, small adjusting screw 5, fixed block 6, small clamping block 7, large clamping surface 8. Small clamping surface 9, the lower end of the slide rail 1 is installed on the fixture seat, the upper end of the slide rail 1 is stuck on the concave edge of the lower end of the moving block 3, and the large adjusting screw 2 is engaged with the moving block 3 , the lower end of the large clamping block 4 is pressed on the concave edge of the upper end of the moving block 3, the upper end of the large clamping block 4 is provided with a groove, the vertical section of the upper part of the groove is rectangular, and the lower part of the groove is a dovetail groove, The fixed block 6 is fixed on the side end of the groove of the large clamping block 4, the upper end of the ...
PUM
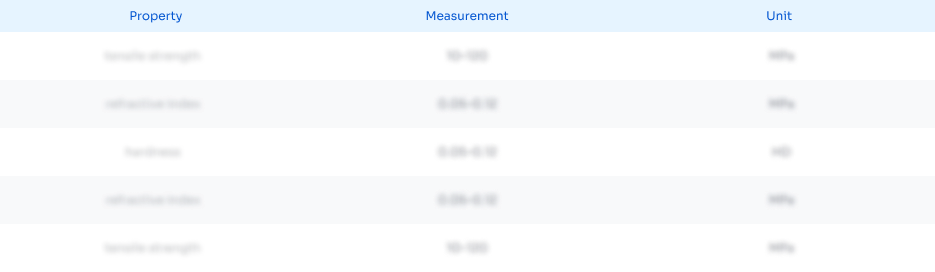
Abstract
Description
Claims
Application Information

- R&D
- Intellectual Property
- Life Sciences
- Materials
- Tech Scout
- Unparalleled Data Quality
- Higher Quality Content
- 60% Fewer Hallucinations
Browse by: Latest US Patents, China's latest patents, Technical Efficacy Thesaurus, Application Domain, Technology Topic, Popular Technical Reports.
© 2025 PatSnap. All rights reserved.Legal|Privacy policy|Modern Slavery Act Transparency Statement|Sitemap|About US| Contact US: help@patsnap.com