Common mode manufacturing method for automobile covering part
A technology for automobile cover parts and a production method, which is applied in the field of casting technology, can solve the problems of high investment cost, low utilization rate of parts and materials, increased personnel and equipment investment, etc. Effect
- Summary
- Abstract
- Description
- Claims
- Application Information
AI Technical Summary
Problems solved by technology
Method used
Image
Examples
Embodiment Construction
[0023] Figure 1 shows a co-molding production method for automotive panels, including drawing, trimming and punching, flanging and shaping and side cutting.
[0024] This process technology is aimed at side wall inner panel parts, and the specific steps are as follows:
[0025] 1. Drawing: use a square plate of 0.7mm×1780mm×1365mm to stretch out the basic shape of the part;
[0026] 2. Trimming and punching: Punching off the peripheral and intermediate shape holes of the parts and the excessive holes to be processed in the subsequent sequence;
[0027] 3. Flanging shaping: Reshape the position with high requirements and small R angle, and flanging the supporting position and surrounding shape of the glue;
[0028] 4. Reshaping side cutting: cut off the incomplete edge trimming around the pre-order, trim the parts partially, punch process holes, positioning holes and installation holes, and separate the two parts from different positions for storage.
[0029] To sum up: this ...
PUM
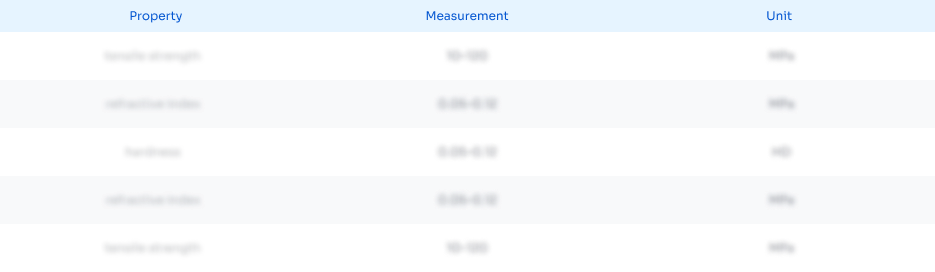
Abstract
Description
Claims
Application Information

- Generate Ideas
- Intellectual Property
- Life Sciences
- Materials
- Tech Scout
- Unparalleled Data Quality
- Higher Quality Content
- 60% Fewer Hallucinations
Browse by: Latest US Patents, China's latest patents, Technical Efficacy Thesaurus, Application Domain, Technology Topic, Popular Technical Reports.
© 2025 PatSnap. All rights reserved.Legal|Privacy policy|Modern Slavery Act Transparency Statement|Sitemap|About US| Contact US: help@patsnap.com