Centrifugal casting method for thin-working layer composite cast iron roll
A cast iron roll and centrifugal casting technology, which is applied in the field of roll casting, can solve the problems of high alloy content in the bonding layer, the influence of punching holes on the roll body, and high hardness, and achieve the effect of low hardness and easy punching operations
- Summary
- Abstract
- Description
- Claims
- Application Information
AI Technical Summary
Problems solved by technology
Method used
Examples
Embodiment 1
[0017] A centrifugal casting method for a composite cast iron roll with a thin working layer. The composite cast iron roll with a thin working layer includes a working layer, a bonding layer and a core arranged sequentially from the outside to the inside. Layer pouring method, the specific centrifugal pouring method is as follows:
[0018] a. Prepare the raw materials and smelt the molten iron according to the composition of the working layer and the bonding layer respectively, and carry out the modification treatment on the molten iron in the working layer and the molten iron in the bonding layer respectively; after the nodular cast iron used in the core is smelted, it is spheroidized and inoculation treatment.
[0019] The composition of the above bonding layer and the weight percentage of each component are as follows: C1.4~1.5, Si0.9~1.0, Mn0.1~0.2, P0.02, S0.03, Cr0.12~0.15, Ni0.24 ~0.3, Mo0.12~0.2; the composition of the working layer and the weight percentage of each c...
Embodiment 2
[0025] The difference between this embodiment and embodiment 1 is the following four points:
[0026] One: The bonding layer adopts four-layer pouring method.
[0027] Second: the thickness ratio of the solidified molten iron in the working layer to the thickness of the first layer of the bonding layer after solidification is 0.5:1, and the thickness ratio of the solidified thickness of the other layers of the bonding layer to the thickness of the previous layer of molten iron is 1: 0.8.
[0028] Third: pour the next layer of molten iron when the inner surface temperature of each layer is 30°C below the freezing point.
[0029] Fourth: The composition of the bonding layer and the weight percentage of each component are as follows: C1.6~1.8, Si1.2~1.4, Mn0.25~0.3, P≤0.1, S≤0.03, Cr0.18~0.2, Ni0 .35~0.4, Mo0.24~0.3; the composition of the working layer and the weight percentage of each component are as follows: C: 3.0~3.1, Si1.5~1.8, Mn0.5~0.6, P≤0.05, S≤0.01 , Cr1.0~1.8, Ni2...
Embodiment 3
[0032] The difference between this example and Example 1 is that the composition of the bonding layer and the weight percentage of each component are as follows: C1.4~1.6, Si1.1~1.2, Mn0.2~0.28, P≤0.05, S≤ 0.02, Cr0.05~0.1, Ni0.3~0.36, Mo0.2~0.25; the composition of the working layer and the weight percentage of each component are as follows: C: 3.2~3.3, Si2.0~2.2, Mn0.8~ 1.0, P0.06, S0.02, Cr2.0-2.5, Ni3.0-4.0, Mo1.0-1.4.
[0033]After testing, the composition and weight percentage of each component of the thin working layer composite cast iron roll produced and prepared are: C1.48, Si1.15, Mn0.25, P0.04, S0.01, Cr0.08, Ni0.32 , Mo0.21; the composition of the working layer and the weight percentage of each component are as follows: C3.26, Si2.1, Mn0.9, P0.04, S0.018, Cr2.2, Ni3.6, Mo1.32 . The hardness of the bonding layer is: 42HSD.
PUM
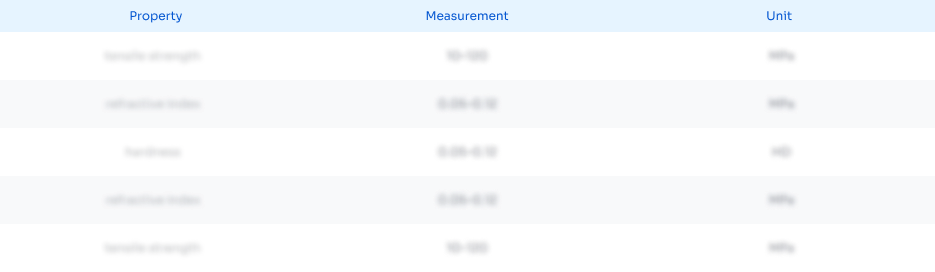
Abstract
Description
Claims
Application Information

- Generate Ideas
- Intellectual Property
- Life Sciences
- Materials
- Tech Scout
- Unparalleled Data Quality
- Higher Quality Content
- 60% Fewer Hallucinations
Browse by: Latest US Patents, China's latest patents, Technical Efficacy Thesaurus, Application Domain, Technology Topic, Popular Technical Reports.
© 2025 PatSnap. All rights reserved.Legal|Privacy policy|Modern Slavery Act Transparency Statement|Sitemap|About US| Contact US: help@patsnap.com