High-speed electric spindle power-heat coupling modeling method
A technology of high-speed electric spindle and modeling method, which is applied in the direction of electric digital data processing, instrumentation, calculation, etc., and can solve problems such as the inability to predict the performance of the spindle, calculation errors, and high joint surface errors of the model.
- Summary
- Abstract
- Description
- Claims
- Application Information
AI Technical Summary
Problems solved by technology
Method used
Image
Examples
Embodiment Construction
[0067] In order to make the object, technical solution and advantages of the present invention clearer, the present invention will be further described in detail below in conjunction with the accompanying drawings and embodiments. It should be understood that the specific embodiments described here are only used to explain the present invention, not to limit the present invention. In addition, the technical features involved in the various embodiments of the present invention described below can be combined with each other as long as they do not constitute a conflict with each other.
[0068] Such as figure 1 As shown, the high-speed electric spindle force-thermal coupling modeling method of the present invention includes the following steps:
[0069] (1) Obtain the engineering parameters of the surface to be combined between the bearing and the main shaft, and the surface to be combined between the main shaft and the bearing, and use fractal contact theory and Hertz contact ...
PUM
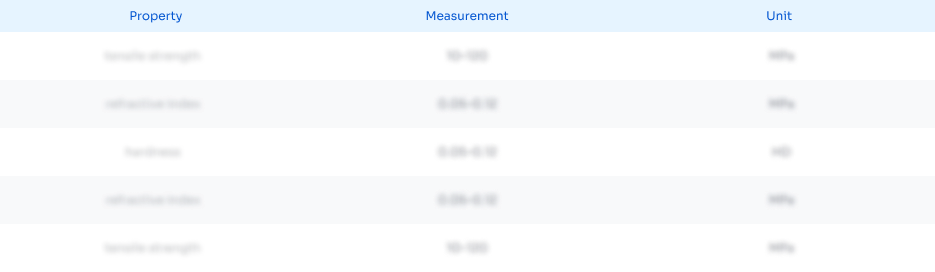
Abstract
Description
Claims
Application Information

- Generate Ideas
- Intellectual Property
- Life Sciences
- Materials
- Tech Scout
- Unparalleled Data Quality
- Higher Quality Content
- 60% Fewer Hallucinations
Browse by: Latest US Patents, China's latest patents, Technical Efficacy Thesaurus, Application Domain, Technology Topic, Popular Technical Reports.
© 2025 PatSnap. All rights reserved.Legal|Privacy policy|Modern Slavery Act Transparency Statement|Sitemap|About US| Contact US: help@patsnap.com