Device for blending catalytic slurry oil in delayed coking technology and method thereof
A technology of delayed coking and catalytic oil slurry, which is applied in the field of delayed coking technology, can solve the problems of affecting residual oil, reducing the heat of coking and cracking, and reducing the outlet temperature of heating furnace, so as to enhance partial upgrading, improve overall benefit, and improve process The effect of material temperature
- Summary
- Abstract
- Description
- Claims
- Application Information
AI Technical Summary
Problems solved by technology
Method used
Image
Examples
Embodiment 1
[0034] A device for blending catalytic oil slurry in delayed coking process, comprising separately established oil slurry tank m, oil slurry pump o, oil slurry heating furnace n, the three are connected in sequence, the outlet of oil slurry heating furnace n is connected to the delayed coking device slag The outlet of oil heating furnace b is connected.
[0035] By setting forth the working method of this device, the present invention can be better understood:
[0036] The residual oil 1 is fed into the raw material buffer tank a, pumped out by the raw material oil pump l, enters the fractionation tower e through the heat exchanger g, and then pumped out by the heating furnace feed pump f and sent to the residual oil heating furnace b to be heated to 490-500 °C; The slurry 2 feeds into the slurry tank m, is pumped out by the slurry pump o and sent to the slurry heating furnace n to be heated to 510-550°C; the high temperature coking oil 5 at the outlet of the residual oil heat...
PUM
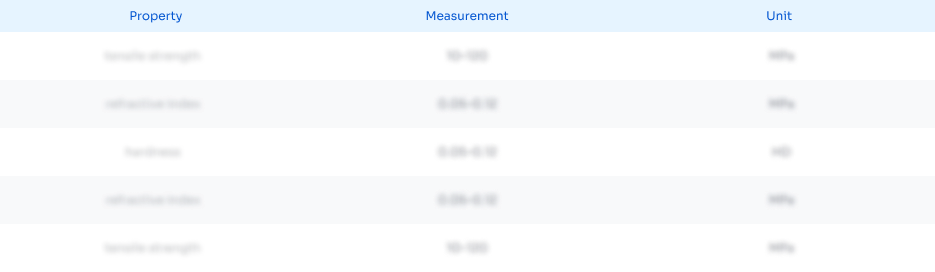
Abstract
Description
Claims
Application Information

- R&D Engineer
- R&D Manager
- IP Professional
- Industry Leading Data Capabilities
- Powerful AI technology
- Patent DNA Extraction
Browse by: Latest US Patents, China's latest patents, Technical Efficacy Thesaurus, Application Domain, Technology Topic, Popular Technical Reports.
© 2024 PatSnap. All rights reserved.Legal|Privacy policy|Modern Slavery Act Transparency Statement|Sitemap|About US| Contact US: help@patsnap.com