Method for converting yttrium oxide into yttrium acetate crystal
A technology of yttrium oxide and yttrium acetate, which is applied in the direction of carboxylate preparation, etc., can solve the problems of complex production process, low production efficiency and high production cost, and achieve the effect of high purity, high production efficiency and pure color
- Summary
- Abstract
- Description
- Claims
- Application Information
AI Technical Summary
Problems solved by technology
Method used
Examples
Embodiment 1
[0023] The method that yttrium oxide is converted into yttrium acetate crystal may further comprise the steps:
[0024] A. Pump analytically pure glacial acetic acid and deionized water into the reaction kettle at a volume ratio of 1:1, stir evenly and heat to boiling;
[0025] B. Rotate the stirring paddle and slowly add the weighed yttrium oxide with a purity of 99.999% into the reaction kettle. The molar ratio of the added amount of yttrium oxide to acetic acid is 1:3.9, and the stirring paddle speed is 70 rpm; It can’t be too fast, too fast consumes energy, and it can’t be too slow, too slow will affect the reaction speed of materials. According to the experimental data, usually the best stirring speed is 60 to 80 revolutions per minute;
[0026] C. After the complete reaction, stop heating when heating the liquid material to 120°C, and let the liquid material in the reactor cool and crystallize naturally. During the cooling process, the stirring paddle continues to stir; ...
Embodiment 2
[0031] The method that yttrium oxide is converted into yttrium acetate crystal may further comprise the steps:
[0032] A. Pump analytically pure glacial acetic acid and deionized water into the reaction kettle at a volume ratio of 1:1, stir evenly and heat to boiling;
[0033] B. Rotate the stirring paddle and slowly add the weighed yttrium oxide with a purity of 99.999% into the reaction kettle, the molar ratio of the added amount of yttrium oxide to acetic acid is 1:3.9, and the rotation speed of the stirring paddle is 60 rpm;
[0034] C. After complete reaction, stop heating when heating the liquid material to 110°C, and use artificial rapid cooling to make the liquid material in the reactor crystallize rapidly. During the cooling process, the stirring paddle continues to stir;
[0035] D. When the temperature of the liquid material is cooled below 50°C, the agitator stops stirring, and the liquid material is discharged into the filter box and the liquid is filtered;
[0...
PUM
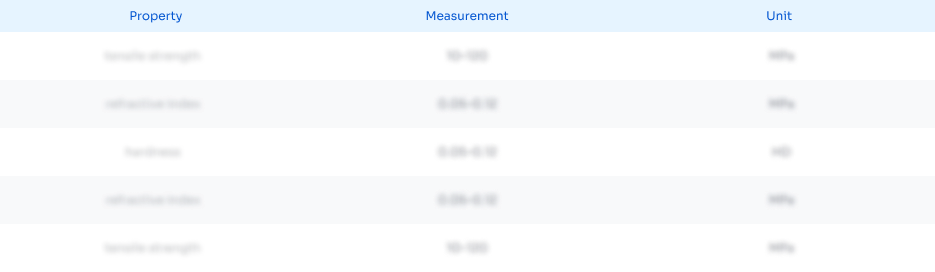
Abstract
Description
Claims
Application Information

- Generate Ideas
- Intellectual Property
- Life Sciences
- Materials
- Tech Scout
- Unparalleled Data Quality
- Higher Quality Content
- 60% Fewer Hallucinations
Browse by: Latest US Patents, China's latest patents, Technical Efficacy Thesaurus, Application Domain, Technology Topic, Popular Technical Reports.
© 2025 PatSnap. All rights reserved.Legal|Privacy policy|Modern Slavery Act Transparency Statement|Sitemap|About US| Contact US: help@patsnap.com