In-situ indentation mechanical testing device based on tensile compression and fatigue combined load mode
A composite load and testing device technology, which is applied in the direction of testing material strength by applying repetitive force/pulsation force, testing material strength by applying stable tension/compression, testing material hardness, etc. Performance testing, single load and other issues, to achieve the effect of compact structure, low cost and high precision
- Summary
- Abstract
- Description
- Claims
- Application Information
AI Technical Summary
Problems solved by technology
Method used
Image
Examples
Embodiment Construction
[0024] The detailed content of the present invention and its specific implementation will be further described below in conjunction with the accompanying drawings.
[0025] see Figure 1 to Figure 5 As shown, the in-situ indentation mechanical testing device based on tension-compression and fatigue composite load mode of the present invention includes a precision drive unit, tension-compression, fatigue composite load unit, indentation load unit, and precision sensing detection unit. The precision drive unit is composed of a DC servo motor 1, a worm 3 and a worm gear 4. The DC servo motor 1 is supported by a motor base 2, and the motor base 2 is fixed on one side of the base 32 by screws III 35, and its output shaft is fixedly connected with the worm 3. Drive the worm gear 4 to rotate, and drive with a large reduction ratio, which can realize quasi-static loading;
[0026] The tension-compression and fatigue composite load unit includes a tension-compression load module and a...
PUM
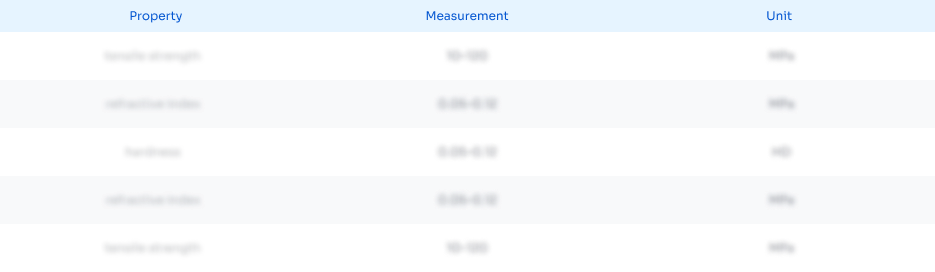
Abstract
Description
Claims
Application Information

- R&D
- Intellectual Property
- Life Sciences
- Materials
- Tech Scout
- Unparalleled Data Quality
- Higher Quality Content
- 60% Fewer Hallucinations
Browse by: Latest US Patents, China's latest patents, Technical Efficacy Thesaurus, Application Domain, Technology Topic, Popular Technical Reports.
© 2025 PatSnap. All rights reserved.Legal|Privacy policy|Modern Slavery Act Transparency Statement|Sitemap|About US| Contact US: help@patsnap.com