Compound imbibing core for thermal column array steam main line and manufacturing method thereof
A technology of liquid-absorbing cores and main channels, which is applied in the field of liquid-absorbing cores, can solve the problems of poor repeatability of manufacturing process, increased liquid return resistance, and small capillary pressure, and achieve the advantages of strong angle adaptability, increased capillary pressure, and enhanced reflux speed Effect
- Summary
- Abstract
- Description
- Claims
- Application Information
AI Technical Summary
Problems solved by technology
Method used
Image
Examples
Embodiment Construction
[0027] In order to better understand the present invention, the specific implementation method of the present invention will be further described below in conjunction with the accompanying drawings, but the implementation method of the present invention is not limited thereto.
[0028] Such as Figure 1a , Figure 1b As shown, a hot column array steam channel composite liquid absorbent core, the composite liquid absorbent core is a cylindrical structure, including the steam main channel and capillary layer; the capillary layer is a multi-section copper powder sintered capillary layer stacked along the axial direction of the composite liquid absorbent core , different sections of the capillary layer have different porosity, starting from close to the heat source, the capillary layer porosity is arranged from small to large along the axial gradient of the liquid-absorbing core; the particle size of the copper powder used for sintering is 100-400 mesh; the main steam channel It i...
PUM
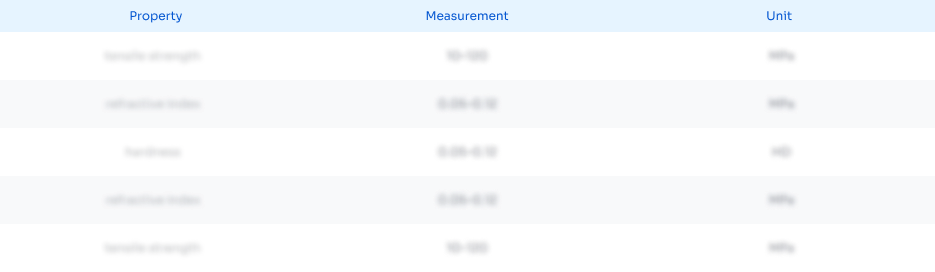
Abstract
Description
Claims
Application Information

- R&D
- Intellectual Property
- Life Sciences
- Materials
- Tech Scout
- Unparalleled Data Quality
- Higher Quality Content
- 60% Fewer Hallucinations
Browse by: Latest US Patents, China's latest patents, Technical Efficacy Thesaurus, Application Domain, Technology Topic, Popular Technical Reports.
© 2025 PatSnap. All rights reserved.Legal|Privacy policy|Modern Slavery Act Transparency Statement|Sitemap|About US| Contact US: help@patsnap.com