Rock powdery emulsion explosive and preparation method thereof
A technology of powdery emulsion explosives and rocks, which is applied in the direction of explosives, etc., can solve problems such as high energy consumption of spray powder, increased safety risks, explosives that cannot meet the quality standards of rock powdery emulsion explosives and industry technical progress guidance.
- Summary
- Abstract
- Description
- Claims
- Application Information
AI Technical Summary
Problems solved by technology
Method used
Examples
Embodiment 1
[0013] Example 1: The raw material composition (% by weight) of rock powdery emulsion explosive is: 90% ammonium nitrate, 0.3% surfactant, 4.0% composite oil phase, and 6.0% porous ammonium nitrate.
[0014] Preparation of water phase: Dissolving ammonium nitrate and water at a ratio of 92% and 8%, with a melting temperature of 120°C; preparation of oil phase: melting temperature of 105°C, and the products prepared according to the above preparation method have been tested by the national safety production Huaibei civil blasting equipment The test results of the inspection center are: the working capacity is 339ml, the toxic gas content is 40L / kg, the impact sensitivity is 10%, and the friction sensitivity is 0%.
Embodiment 2
[0015] Example 2: The raw material composition (% by weight) of rock powdery emulsion explosive is: 92% ammonium nitrate, 0.4% surfactant, 5.0% composite oil phase, and 3.0% porous ammonium nitrate.
[0016] Preparation of water phase: Dissolving ammonium nitrate and water at a ratio of 92% and 8%, the melting temperature is 120°C; preparation of oil phase: melting temperature is 105°C, and the products prepared according to the above preparation method have passed the National Civil Explosive Equipment Quality Supervision and Inspection Center The test results are: working capacity 367ml, toxic gas content 48L / kg, impact sensitivity 0%, friction sensitivity 0%.
PUM
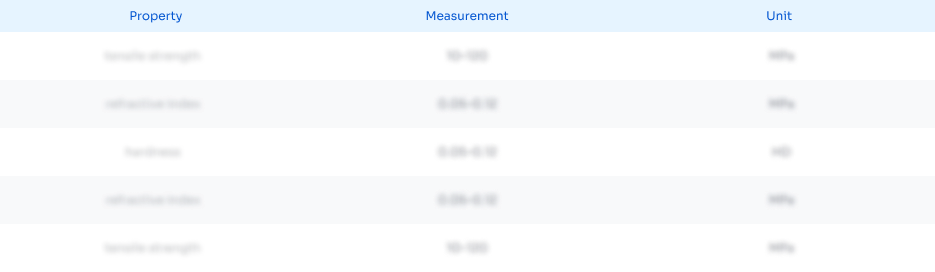
Abstract
Description
Claims
Application Information

- Generate Ideas
- Intellectual Property
- Life Sciences
- Materials
- Tech Scout
- Unparalleled Data Quality
- Higher Quality Content
- 60% Fewer Hallucinations
Browse by: Latest US Patents, China's latest patents, Technical Efficacy Thesaurus, Application Domain, Technology Topic, Popular Technical Reports.
© 2025 PatSnap. All rights reserved.Legal|Privacy policy|Modern Slavery Act Transparency Statement|Sitemap|About US| Contact US: help@patsnap.com