Perforated molybdenum piercing head structural member
A technology for structural parts and plugs, applied in metal processing equipment, metal rolling, manufacturing tools, etc., can solve the problems of reduced service life of the plug, failure of the plug, increased consumption of auxiliary materials, etc. quality, and the effect of improving the service life
- Summary
- Abstract
- Description
- Claims
- Application Information
AI Technical Summary
Problems solved by technology
Method used
Image
Examples
Embodiment 1
[0019] Example 1 : To produce capillary tubes with a diameter of Φ78mm and a wall thickness of 7.25mm, the corresponding perforated molybdenum plug structure is made as follows:
[0020] 1) Plug 1 is made of all molybdenum material: diameter Φ59mm, length 160mm, which is 10mm longer than the existing plug;
[0021] 2) Perforation area L of plug 1 1 The length is set at 80mm, and the rolling area L 2 The length is set at 70mm, rolling area L 2 Length / perforated area L 1 The length ratio is 87.5%, and the circular area L 3 The length is 10mm. Perforated area L 1 The shape is conical, and the rolling area L 2 The shape is cylindrical. Compared figure 1 , head 1 perforated area L 1 The length is obviously shortened, the "belly shape" is increased, and the wear thickness of the top layer of the plug 1 is virtually increased, and the service life of the plug 1 is undoubtedly increased. Rolling area L 2 The length increases, and the lengthening of the length is beneficia...
Embodiment 2
[0023] Example 2: To produce capillary tubes with a diameter of Φ102mm and a wall thickness of 7.5mm, the corresponding perforated molybdenum plug structure is made as follows:
[0024] 1) Plug 1 is made of all molybdenum material: diameter Φ80mm, length 190mm, 10mm longer than the existing plug;
[0025] 2) Perforation area L of plug 1 1 The length is set at 100mm, and the rolling area L 2 The length is set at 75mm, rolling area L 2 Length / perforated area L 1 The length ratio is 75%, and the circular area L 3 The length is 15mm. Perforated area L 1 The shape is conical, and the rolling area L 2 The shape is cylindrical;
[0026] 3) The internal structure of the connecting joint 2: the connecting joint 2 is a straight pipe joint with a blind hole at one end, that is, the contact end of the connecting joint 2 and the plug 1 is reserved for 4mm without drilling, the blind end, and the rest are through holes. Since the connecting joint 2 is a large and small head, its ...
Embodiment 3
[0027] Example 3: To produce capillary tubes with a diameter of Φ170mm and a wall thickness of 8mm, the corresponding perforated molybdenum plug structure is made as follows:
[0028] 1) Plug 1 is made of all molybdenum material: diameter Φ130mm, length 270mm, 20mm longer than the existing plug;
[0029] 2) Perforation area L of plug 1 1 The length is set at 131.5mm, rolling area L 2 The length is set at 118.5mm, rolling area L 2 Length / perforated area L 1 The length ratio is 90%, and the circular area L3 The length is 20mm. Perforated area L 1 The shape is conical, and the rolling area L 2 The shape is cylindrical;
[0030] 3) The internal structure of the connecting joint 2: the connecting joint 2 is a straight pipe joint with a blind hole at one end, that is, the contact end of the connecting joint 2 and the plug 1 is reserved for 5mm without drilling, the blind end, and the rest are through holes. Since the connecting joint 2 is a large and small head, its inner ...
PUM
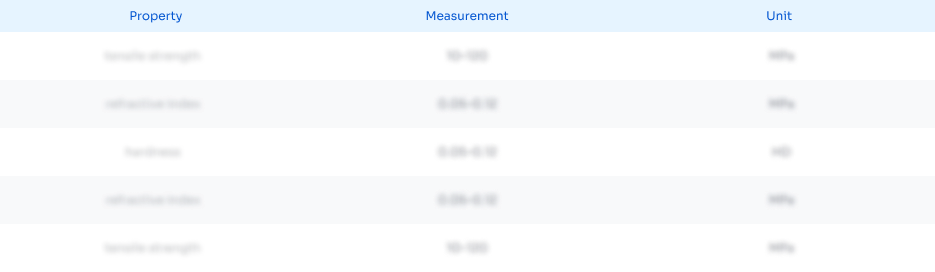
Abstract
Description
Claims
Application Information

- R&D
- Intellectual Property
- Life Sciences
- Materials
- Tech Scout
- Unparalleled Data Quality
- Higher Quality Content
- 60% Fewer Hallucinations
Browse by: Latest US Patents, China's latest patents, Technical Efficacy Thesaurus, Application Domain, Technology Topic, Popular Technical Reports.
© 2025 PatSnap. All rights reserved.Legal|Privacy policy|Modern Slavery Act Transparency Statement|Sitemap|About US| Contact US: help@patsnap.com