Silicon oil preparation method
A technology of silicone oil and high hydrogen-containing silicone oil, which is applied in the field of silicone oil production, can solve the problems of side reactions, long reaction time, and complicated procedures in the polymerization process, and achieve the effects of simple operation, avoiding side reactions, and improving product quality
- Summary
- Abstract
- Description
- Claims
- Application Information
AI Technical Summary
Problems solved by technology
Method used
Image
Examples
Embodiment 1
[0032] At 30°C, add 25 parts of D4 (I), 2 parts of hexamethyldisiloxane according to (II) and 5 parts of hydrogen-containing silicone oil (III) into mixing kettle 1 in proportion, and pre-mix for 30 minutes. During the mixing process Heat the raw material to 40-80°C, pass the metering pump 2 at a rate of 1-20m 3 / h flow rate to transfer the pre-mixed raw materials to the catalytic bed 3, the pressure of the pre-mixture passing through the resin catalytic bed 3 is kept at 1MPa, and the contact time is kept at 6h. (IV).
Embodiment 2
[0034] At 20°C, add 40 parts of D4 (I) and 2 parts of tetramethyldisiloxane (V) into the mixing kettle 1 in proportion, and pre-mix for 30 minutes. During the mixing process, the raw materials are heated to 40-80°C. Metering pump 2 is 1~20m 3 / h flow rate transfers the pre-mixed raw material to the catalytic bed 3, the pre-mixture is kept at 0.85MPa by the resin catalytic bed pressure, and the contact time is maintained at 8h, and the product obtained by the reaction is collected by the collection tank 4, which is terminal hydrogen silicone oil ( VI).
Embodiment 3
[0036] At 45°C, add 20 parts of D4 (I) and 5 parts of heptamethyltrisiloxane (VII) into mixing kettle 1 in proportion, and pre-mix for 30 minutes. During the mixing process, the raw materials are heated to 40-80°C, and the metering pump 2 is used for 1-20m 3 The premixed raw material is transferred to the catalytic bed 3 at a flow rate of / h. The pressure of the premixed resin catalytic bed is kept at 1.2MPa, and the contact time is kept at 4h. (VIII).
PUM
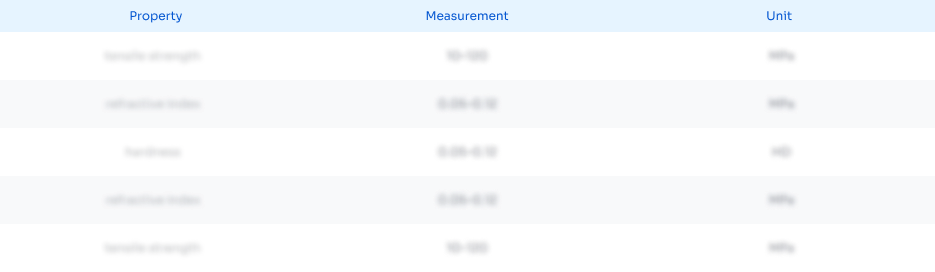
Abstract
Description
Claims
Application Information

- R&D
- Intellectual Property
- Life Sciences
- Materials
- Tech Scout
- Unparalleled Data Quality
- Higher Quality Content
- 60% Fewer Hallucinations
Browse by: Latest US Patents, China's latest patents, Technical Efficacy Thesaurus, Application Domain, Technology Topic, Popular Technical Reports.
© 2025 PatSnap. All rights reserved.Legal|Privacy policy|Modern Slavery Act Transparency Statement|Sitemap|About US| Contact US: help@patsnap.com