Novel acidic molybdenum aluminum molybdenum etching liquid and its preparation process
A preparation process and etching solution technology, which is applied in the field of new acidic molybdenum aluminum molybdenum etching solution and preparation process, can solve the problem of affecting the image accuracy and quality of high-density thin wires, affecting product yield, difficult to control etching angle and etching of different metal layers Quantity and other issues, to achieve the effect of stable reaction, smooth lines and clean surface
- Summary
- Abstract
- Description
- Claims
- Application Information
AI Technical Summary
Problems solved by technology
Method used
Examples
Embodiment 1
[0025] (1) Composition and preparation of new acidic molybdenum-aluminum-molybdenum etching solution
[0026] The novel acidic molybdenum-aluminum-molybdenum etching solution includes phosphoric acid, acetic acid, nitric acid, cationic surfactant, metal nitrate and pure water. The raw material weight percentages of the molybdenum-aluminum-molybdenum etching solution are respectively: phosphoric acid 60%, acetic acid 8%, nitric acid 7% %, metal nitrate 1%, cationic surfactant 0.5%, and the rest is pure water.
[0027] Wherein, the metal nitrate is potassium nitrate, and the purity of the potassium nitrate is higher than 99.5%.
[0028] Wherein, the concentrations of phosphoric acid, acetic acid and nitric acid are respectively: phosphoric acid 84%, acetic acid 99.5%, nitric acid 68%.
[0029] Wherein, the cationic surfactant is polyacrylamide.
[0030] Wherein, in the molybdenum-aluminum-molybdenum etching solution, there are 800 particles with a particle size greater than 0....
Embodiment 2
[0047] The novel acidic molybdenum-aluminum-molybdenum etching solution comprises phosphoric acid, acetic acid, nitric acid, cationic surfactant, metal nitrate and pure water, and the raw material weight percents of described molybdenum-aluminum-molybdenum etching solution are respectively: phosphoric acid 65%, acetic acid 11%, nitric acid 4% %, metal nitrate 0.3%, cationic surfactant 0.1%, and the rest is pure water.
[0048] Wherein, the metal nitrate is potassium nitrate, and the purity of the potassium nitrate is higher than 99.5%.
[0049] Wherein, the concentrations of phosphoric acid, acetic acid and nitric acid are respectively: phosphoric acid 84%, acetic acid 99.5%, nitric acid 68%.
[0050] Wherein, the cationic surfactant is benzalkonium chloride.
[0051] Wherein, in the molybdenum-aluminum-molybdenum etching solution, there are 700 particles with a particle size greater than 0.3 μm per 1000 kg, impurity cations are 25 ppb, and impurity anions are 0.02 ppb.
[0...
Embodiment 3
[0055] The novel acidic molybdenum-aluminum-molybdenum etching solution comprises phosphoric acid, acetic acid, nitric acid, cationic surfactant, metal nitrate and pure water, and the raw material weight percentages of the molybdenum-aluminum-molybdenum etching solution are respectively: phosphoric acid 70%, acetic acid 15%, nitric acid 1 %, metal nitrate 0.1%, cationic surfactant 0.001%, and the rest is pure water.
[0056] Wherein, the metal nitrate is potassium nitrate, and the purity of the potassium nitrate is higher than 99.5%.
[0057]Wherein, the concentrations of phosphoric acid, acetic acid and nitric acid are respectively: phosphoric acid 84%, acetic acid 99.5%, nitric acid 68%.
[0058] Wherein, the cationic surfactant is benzalkonium bromide.
[0059] Wherein, in the molybdenum-aluminum-molybdenum etching solution, there are 500 particles with a particle size greater than 0.3 μm per 1000 kg, impurity cations are 20 ppb, and impurity anions are 0.03 ppb.
[0060]...
PUM
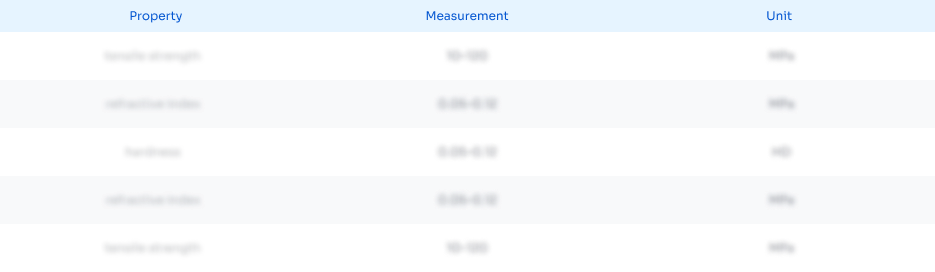
Abstract
Description
Claims
Application Information

- R&D Engineer
- R&D Manager
- IP Professional
- Industry Leading Data Capabilities
- Powerful AI technology
- Patent DNA Extraction
Browse by: Latest US Patents, China's latest patents, Technical Efficacy Thesaurus, Application Domain, Technology Topic, Popular Technical Reports.
© 2024 PatSnap. All rights reserved.Legal|Privacy policy|Modern Slavery Act Transparency Statement|Sitemap|About US| Contact US: help@patsnap.com