Production method of electrochemical active pole piece
A technology for active pole pieces and manufacturing methods, which is applied to battery electrodes, electrode carriers/collectors, circuits, etc., can solve problems such as weak power performance of lithium-ion batteries, improve battery rate charge and discharge capabilities and cycle life, and reduce battery life. Internal resistance, effect of improving tensile strength
- Summary
- Abstract
- Description
- Claims
- Application Information
AI Technical Summary
Problems solved by technology
Method used
Image
Examples
Embodiment 1
[0030] Put the aluminum foil current collector with ordered three-dimensional square holes and regular arrangement of round holes in an ultrasonic tank for cleaning for 15 minutes, and dry it for later use. Then, weigh lithium iron phosphate, carbon black, polyvinylidene fluoride, and N-methyl-2-pyrrolidone according to the ratio of 100, 0.5, 3, and 125, and add them to the uniformly dispersed 1% graphene suspension in turn, Ultrasonic dispersion for 30 minutes, followed by high-speed shearing for 30 minutes to form a slurry, and then ball milling for 15 minutes to obtain a uniformly dispersed graphene / active material composite electrode slurry. Next, the above-mentioned composite electrode slurry is coated on a clean current collector with a three-dimensional square hole structure, and dried by infrared. Then, a porous film layer was coated on both sides of the active pole piece, and then rolled into a 360mm×180mm×2mm pole piece sample for lithium ion batteries.
[0031] fi...
Embodiment 2
[0033] The aluminum foil current collector with an ordered three-dimensional square hole structure was placed in an ultrasonic bath for cleaning for 15 minutes, and dried for later use. Then, weigh lithium iron phosphate, carbon black, polyvinylidene fluoride, and N-methyl-2-pyrrolidone in proportions of 100, 1.5, 3, and 130, and add them successively to a uniformly dispersed 0.5% graphene suspension, Ultrasonic dispersion for 30 minutes, followed by high-speed shearing for 30 minutes to form a slurry, and then ball milling for 15 minutes to obtain a uniformly dispersed graphene / active material composite electrode slurry. Next, the above-mentioned composite electrode slurry is coated on a clean current collector with a three-dimensional square hole structure, and dried by infrared. Then, a porous film layer was coated on both sides of the active pole piece, and then rolled into a 360mm×180mm×2mm pole piece sample for lithium ion batteries.
Embodiment 3
[0035] The aluminum foil current collector with an ordered three-dimensional circular hole structure was placed in an ultrasonic tank for cleaning for 15 minutes, and dried for later use. Then, weigh lithium iron phosphate, carbon black, polyvinylidene fluoride, and N-methyl-2-pyrrolidone according to the ratio of 100, 1, 3, and 125, and add them to the uniformly dispersed 1% graphene suspension in turn, Ultrasonic dispersion for 30 minutes, followed by high-speed shearing for 30 minutes to form a slurry, and then ball milling for 15 minutes to obtain a uniformly dispersed graphene / active material composite electrode slurry. Next, the above-mentioned composite electrode slurry is coated on a clean current collector with a three-dimensional square hole structure, and dried by infrared. Then, a porous film layer was coated on both sides of the active pole piece, and then rolled into a 360mm×180mm×2mm pole piece sample for lithium ion batteries.
PUM
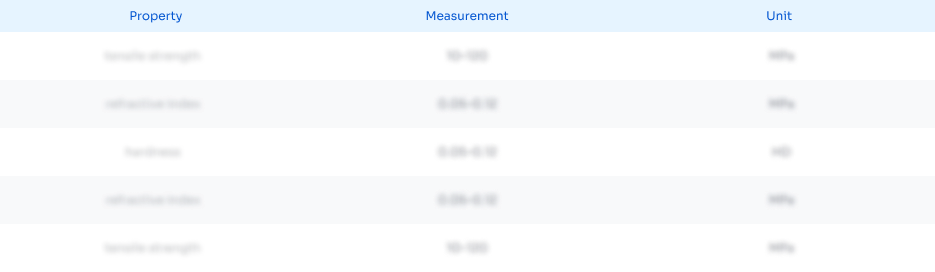
Abstract
Description
Claims
Application Information

- R&D
- Intellectual Property
- Life Sciences
- Materials
- Tech Scout
- Unparalleled Data Quality
- Higher Quality Content
- 60% Fewer Hallucinations
Browse by: Latest US Patents, China's latest patents, Technical Efficacy Thesaurus, Application Domain, Technology Topic, Popular Technical Reports.
© 2025 PatSnap. All rights reserved.Legal|Privacy policy|Modern Slavery Act Transparency Statement|Sitemap|About US| Contact US: help@patsnap.com