A method and device for vacuum hot-dip aluminum or aluminum alloy plating on metal workpieces
A metal workpiece, hot-dip aluminum plating technology, applied in hot-dip plating process, metal material coating process, coating, etc., can solve problems that affect surface quality and corrosion resistance, cannot stop production at any time, and are difficult to produce. Achieve the effects of avoiding surface oxidation, increasing interface bonding force, and reducing molten salt consumption
- Summary
- Abstract
- Description
- Claims
- Application Information
AI Technical Summary
Problems solved by technology
Method used
Image
Examples
Embodiment Construction
[0036] The present invention is described in detail below by way of examples.
[0037] Such as figure 1 As shown, a vacuum hot-dip aluminum and aluminum alloy device for metal workpieces consists of a vacuum pump 1, a reversing valve 2, a reduction furnace exhaust pipe 3, a cooling furnace exhaust pipe 4, an air intake valve 5, a cooling water outlet 6, Connecting bolt 7, winch motor 8, steel wire rope 9, feeding mechanism 10, material pan 11, upper exhaust valve 12, cooling furnace 13, cooling wall 15, cooling water inlet 16, sealing valve cover 17, driving shaft 18, reduction Furnace 19, heating element 20, reduction furnace insulation layer 21, lower exhaust valve 22, molten aluminum liquid 23, aluminum melting furnace 24, heater 25 and aluminum melting furnace insulation layer 26.
[0038] Using the device, the ordinary carbon steel seamless steel pipe (hereinafter referred to as the steel pipe) after hot rolling is used as a metal workpiece for vacuum hot-dip aluminum pl...
PUM
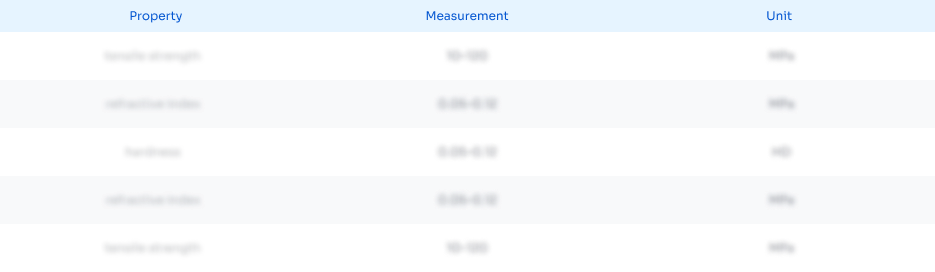
Abstract
Description
Claims
Application Information

- Generate Ideas
- Intellectual Property
- Life Sciences
- Materials
- Tech Scout
- Unparalleled Data Quality
- Higher Quality Content
- 60% Fewer Hallucinations
Browse by: Latest US Patents, China's latest patents, Technical Efficacy Thesaurus, Application Domain, Technology Topic, Popular Technical Reports.
© 2025 PatSnap. All rights reserved.Legal|Privacy policy|Modern Slavery Act Transparency Statement|Sitemap|About US| Contact US: help@patsnap.com