Hexagonal ferrite material with high magnetic loss in L wave band and preparation method thereof
A hexagonal ferrite, L-band technology, applied in the field of materials, can solve the problems such as the mismatch between the wave absorbing coating and the free space impedance, the inability to absorb electromagnetic waves well, and the poor magnetic loss performance, and achieve excellent high-frequency soft magnetic properties. energy, easy mass production, high magnetic loss effect
- Summary
- Abstract
- Description
- Claims
- Application Information
AI Technical Summary
Problems solved by technology
Method used
Image
Examples
preparation example Construction
[0028] The preparation method comprises the following steps:
[0029] 1. Mixed raw materials: the main components and content (mass percentage) of the present invention are calculated as: BaCO 3 : 0.00~23.55wt%, SrCO 3 :0.00~18.75wt%, CoO: 6.68~7.09wt%, Fe 2 o 3 : 69.76~74.15wt%.
[0030] Weigh the raw materials as required, and put them into a ball mill for ball milling. The mass ratio of the ball milled material, zirconia balls, and deionized water is 1:3:1.2, and the mass ratio of large-sized balls (radius about 4.4mm) and small-sized balls (radius about 2.5mm) is 1: 2. The ball milling time is 3 hours, and the rotation speed is set at 300 revolutions per minute. The main purpose of ball milling is to mix raw materials evenly.
[0031] 2. Pre-burning: Dry the ball-milled raw materials, put the dried raw materials into a high-temperature furnace under air or oxygen atmosphere for pre-burning, the pre-burning temperature is 1120-1220 °C, and the heating rate is 3 °C per...
Embodiment 1
[0034] 1. The main components and content (mass percentage) are calculated as oxides:
[0035] Formulation: BaCO 3 : 23.56wt%, SrCO 3 : 0.00wt%, CoO: 6.67wt%, Fe 2 o 3 : 69.76wt%, that is, the chemical composition is: (Ba 1-x Sr x ) 3 co 2 Fe 24 o 41 , where x=0.0.
[0036]2. Mixing and ball milling raw materials: weigh the raw materials according to the requirements, and put them into a ball mill for ball milling. The mass ratio of the ball milled material, zirconia balls, and deionized water is 1:3:1.2, and the mass ratio of large-sized balls (radius about 4.4mm) and small-sized balls (radius about 2.5mm) is 1: 2. The ball milling time is 3 hours, and the rotation speed is set at 300 revolutions per minute. The main purpose of ball milling is to mix raw materials evenly.
[0037] 3. Pre-burning: After drying the ball-milled raw materials, put them into a high-temperature furnace under air atmosphere for pre-burning. The pre-burning temperature is 1170°C, the heat...
Embodiment 2
[0041] 1. The main components and content (mass percentage) are calculated as oxides:
[0042] Formulation: BaCO 3 : 19.08wt%, SrCO 3 : 3.57wt%, CoO: 6.76wt%, Fe 2 o 3 : 70.59wt%, that is, the chemical composition is: (Ba 1-x Sr x ) 3 co 2 Fe 24 o 41 , where x=0.2.
[0043] 2. Mixing and ball milling raw materials: weigh the raw materials according to the requirements, and put them into a ball mill for ball milling. The mass ratio of the ball milled material, zirconia balls, and deionized water is 1:3:1.2, and the mass ratio of large-sized balls (radius about 4.4mm) and small-sized balls (radius about 2.5mm) is 1: 2. The ball milling time is 3 hours, and the rotation speed is set at 300 revolutions per minute. The main purpose of ball milling is to mix raw materials evenly.
[0044] 3. Pre-burning: Dry the ball-milled raw materials, put the dried raw materials into a high-temperature furnace under an air atmosphere for pre-burning, the pre-burning temperature is 11...
PUM
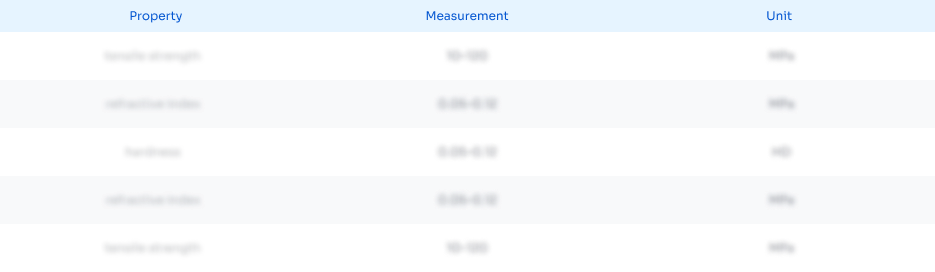
Abstract
Description
Claims
Application Information

- Generate Ideas
- Intellectual Property
- Life Sciences
- Materials
- Tech Scout
- Unparalleled Data Quality
- Higher Quality Content
- 60% Fewer Hallucinations
Browse by: Latest US Patents, China's latest patents, Technical Efficacy Thesaurus, Application Domain, Technology Topic, Popular Technical Reports.
© 2025 PatSnap. All rights reserved.Legal|Privacy policy|Modern Slavery Act Transparency Statement|Sitemap|About US| Contact US: help@patsnap.com