Die and method for rolling tubeless rim plate
A sheet and rim technology is applied in the field of tubeless rim sheet rolling die and rolling to achieve the effects of improving rolling efficiency, increasing bearing capacity and metal utilization rate, and reducing rolling process
- Summary
- Abstract
- Description
- Claims
- Application Information
AI Technical Summary
Problems solved by technology
Method used
Image
Examples
Embodiment Construction
[0017] The present invention will be described in further detail below in conjunction with the accompanying drawings.
[0018] Such as Figure 2-5 As shown, the tubeless rim plate rolling die of the present invention includes multiple stages of rolls, and the multiple stages of rolls are respectively provided with different-shaped passes.
[0019] In the embodiment, there are 4 shifts of the rolls, 12 passes of the pass, and one pass for each pass. The pass includes the first pass type 1, the second pass type 2, the third pass type 3, the fourth pass type 4, the fifth pass type 5, the sixth pass type 6, the seventh pass type 7, and the eighth pass type 8 , the ninth hole type 9, the tenth hole type 10, the eleventh hole type 11 and the twelfth hole type 12; the size of the hole type between the first hole type 1 to the twelfth hole type 12 gradually decrease.
[0020] The middle part of the first pass type 1, the second pass type 2, the third pass type 3 and the ...
PUM
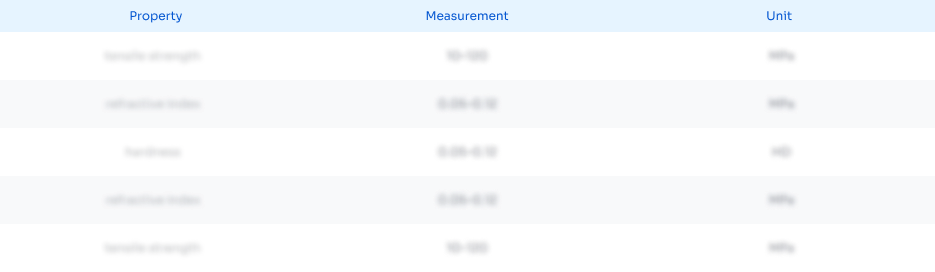
Abstract
Description
Claims
Application Information

- R&D
- Intellectual Property
- Life Sciences
- Materials
- Tech Scout
- Unparalleled Data Quality
- Higher Quality Content
- 60% Fewer Hallucinations
Browse by: Latest US Patents, China's latest patents, Technical Efficacy Thesaurus, Application Domain, Technology Topic, Popular Technical Reports.
© 2025 PatSnap. All rights reserved.Legal|Privacy policy|Modern Slavery Act Transparency Statement|Sitemap|About US| Contact US: help@patsnap.com