Preparation method of injection-use oxaliplatin freeze-dried preparation
The technology of oxaliplatin and freeze-dried preparation is applied in the field of preparation of oxaliplatin freeze-dried powder injection, and can solve the problems of large difference between product temperature and partition temperature, high solution concentration, cracked vial of vial, etc. Achieve the effect of high yield, fast redissolving and slowing down the freezing time
- Summary
- Abstract
- Description
- Claims
- Application Information
AI Technical Summary
Problems solved by technology
Method used
Examples
Embodiment 1
[0020] Taking 50 bottles of oxaliplatin freeze-dried preparation for injection as an example, the specific preparation method is:
[0021] Accurately weigh 22.5g of lactose monohydrate, add 50ml of water for injection, stir at 60-80°C to dissolve. Add 0.1% (w / w) medicinal charcoal to the above solution, heat and stir at 60-80°C for 30 minutes, filter and decarbonize, cool to room temperature, and set aside. Weigh an appropriate amount of water for injection, and inject nitrogen into it to eliminate oxygen in the water. Accurately weigh 2.5g of oxaliplatin, add 425ml of water for injection, stir at 20-30°C to dissolve, and keep nitrogen and light out during the dissolution of the main drug. The obtained oxaliplatin solution is placed for no more than 6 hours under nitrogen-filled and light-shielded conditions, and the above-mentioned lactose solution is added to the oxaliplatin solution, supplemented with water for injection to the full amount, and mixed evenly under light-shi...
Embodiment 2
[0027] Prepare 1.0 g of oxaliplatin solution according to conventional methods, then carry out low-temperature freeze-drying according to the following procedures:
[0028] A. Pre-freezing: adopt the quick-freezing process, first cool down the freeze-drying cabinet to -5~-10°C, and quickly set the temperature of the heat transfer oil to -45°C after the sample enters the cabinet, keep the temperature of the product and the heat transfer oil at the same temperature for 2~3 hours .
[0029] B. Sublimation drying: Raise the temperature of the heat transfer oil to -10°C at a speed of 1°C / 5min. When the temperature of the product and the heat transfer oil are similar, raise the temperature of the heat transfer oil to 0°C at a speed of 2°C / 5min. ℃, the sublimation drying stage ends, and the total time of this process is not less than 15h.
[0030] C. Analytical drying: heat the heat transfer oil at a rate of 2°C / 5min, raise the temperature of the product to 30±2°C, and keep it warm ...
Embodiment 3
[0033] Prepare 1.0 g of oxaliplatin solution according to conventional methods, then carry out low-temperature freeze-drying according to the following procedures:
[0034] A. Pre-freezing: adopt the quick-freezing process, first cool down the freeze-drying cabinet to -5~-10°C, and quickly set the temperature of the heat transfer oil to -45°C after the sample enters the cabinet, keep the temperature of the product and the heat transfer oil at the same temperature for 3-4 hours .
[0035] B. Sublimation drying: Raise the temperature of the heat transfer oil to -10°C at a speed of 1°C / 5min. When the temperature of the product and the heat transfer oil are similar, raise the temperature of the heat transfer oil to 0°C at a speed of 2°C / 5min. ℃, the sublimation drying stage ends, and the total time of this process is not less than 15h.
[0036] C. Analytical drying: heat the heat transfer oil at a rate of 2°C / 5min, raise the temperature of the product to 30±2°C, and keep it warm ...
PUM
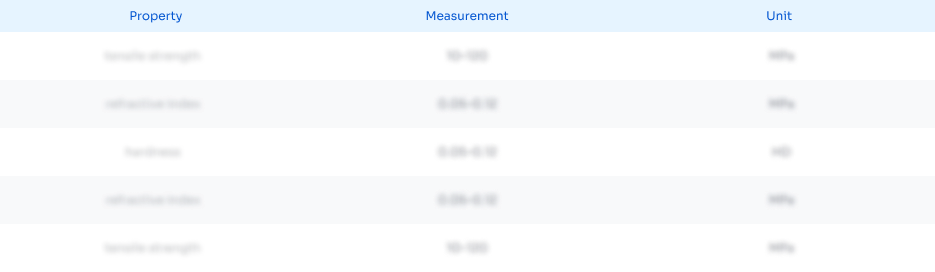
Abstract
Description
Claims
Application Information

- R&D
- Intellectual Property
- Life Sciences
- Materials
- Tech Scout
- Unparalleled Data Quality
- Higher Quality Content
- 60% Fewer Hallucinations
Browse by: Latest US Patents, China's latest patents, Technical Efficacy Thesaurus, Application Domain, Technology Topic, Popular Technical Reports.
© 2025 PatSnap. All rights reserved.Legal|Privacy policy|Modern Slavery Act Transparency Statement|Sitemap|About US| Contact US: help@patsnap.com