Water-reactive al composite material, water-eactive thermally sprayed al film, process for production of thermally sprayed al film, and structural member for film-forming chamber
A composite material and manufacturing method technology, which are applied in the directions of fusion spraying, metal material coating process, sputtering coating, etc., to achieve the effects of improved weather resistance, simple process, and increased number of reuses
- Summary
- Abstract
- Description
- Claims
- Application Information
AI Technical Summary
Problems solved by technology
Method used
Image
Examples
reference example 1
[0054] 4NAl-3.0wt%In-0.1wt%Si (addition amount of In and Si, Al weight basis) obtained by blending 4NAl, In and Si in a predetermined ratio, and uniformly melting In and Si in Al is processed as The rod-shaped spraying material is sprayed by molten rod flame (heat source: C 2 h 2 -O 2 gas, about 3000° C.) is sprayed on the surface of a base material made of aluminum in an air atmosphere to form an Al sprayed film. The Al sprayed coating thus obtained was subjected to heat treatment at 0 to 350° C. (in air, for 1 hour, furnace cooling) instead of the heat history received from the film formation process. The substrate with Al sprayed coating before heat treatment (0°C) and the substrate with Al sprayed coating after heat treatment were immersed in 300ml of deionized water at 80°C, and the current density of the immersion solution was measured. Solubility of Al spray coating.
[0055] As a result, it was found that there is a relationship between the addition of Si and the s...
reference example 2
[0057]Using 4NAl as Al, the effects of adding In and Ti in the following Al-In-Ti compositions (a) to (d) were examined. The amounts of In and Ti added are based on the weight of Al.
[0058] (a) 4NAl-2.1wt%In-0.19wt%Ti
[0059] (b) 4NAl-1.2wt%In-0.18wt%Ti
[0060] (c) 4NAl-1.8wt%In-0.20wt%Ti
[0061] (d) 4NAl-3.0wt%In-0.17wt%Ti
[0062] Al, In, and Ti are blended in a specified ratio, and In and Ti are uniformly melted in Al and processed into a rod-shaped spraying material. 2 h 2 -O 2 gas, about 3000° C.), and sprayed on the surface of the substrate made of aluminum in the air atmosphere to form an Al sprayed film. Heat treatment at 0 to 350° C. (in the atmosphere, 1 hour, furnace cooling) was performed on each of the Al sprayed coatings obtained in this way instead of the heat history received from the film formation process. Substrates with Al sprayed coatings in the state before heat treatment (0°C) and substrates with Al sprayed coatings after heat treatment were ...
Embodiment 1
[0067] 4NAl-3.0wt%In-0.2wt%Si-0.2wt%Ti (In, Si and Ti The amount of addition, Al weight basis) processed into a rod-shaped spraying material, through the fusion rod flame spraying (heat source: C 2 h 2 -O 2 gas, about 3000° C.), in the air atmosphere, sprayed on the surface of the substrate made of aluminum to form an Al sprayed film. For the Al sprayed film (simulated deposited film) obtained in this way, the heat treatment time (0 to 500 hours) at 250°C in the air and the film removal property caused by immersion in 80°C deionized water were studied (film removal time (hours) ) and, for comparison, the film removal property was studied in the same manner as above for the case of an Al sprayed film composed of 5NAl-3.0wt% In (conventional Al sprayed film (simulated deposited film)).
[0068] The results thus obtained are shown in figure 2 . exist figure 2 Among them, the horizontal axis is the heat treatment time (hours) at 250° C., and the vertical axis is the film r...
PUM
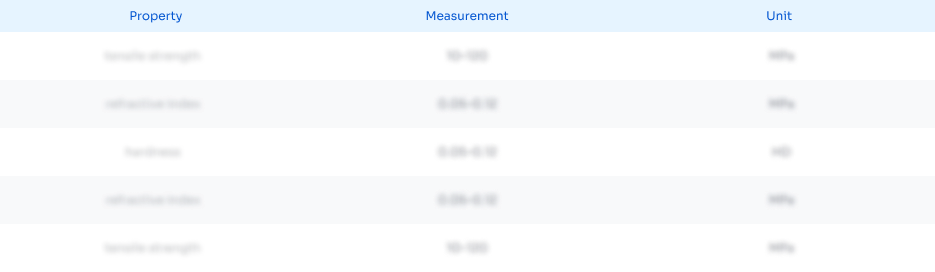
Abstract
Description
Claims
Application Information

- R&D
- Intellectual Property
- Life Sciences
- Materials
- Tech Scout
- Unparalleled Data Quality
- Higher Quality Content
- 60% Fewer Hallucinations
Browse by: Latest US Patents, China's latest patents, Technical Efficacy Thesaurus, Application Domain, Technology Topic, Popular Technical Reports.
© 2025 PatSnap. All rights reserved.Legal|Privacy policy|Modern Slavery Act Transparency Statement|Sitemap|About US| Contact US: help@patsnap.com