Method for making line in direct negative etching way
A production method and direct technology, applied in the direction of removing conductive materials by chemical/electrolytic methods, etc., can solve the problems of unsuitability for mass production, long production process time, large copper usage, etc., to save surface treatment costs and operation. The effect of simplifying and avoiding contamination
- Summary
- Abstract
- Description
- Claims
- Application Information
AI Technical Summary
Problems solved by technology
Method used
Image
Examples
Embodiment 1
[0041] A method for directly etching a circuit on a negative film, comprising the following steps:
[0042] A. Carry out material cutting, edge grinding, filleting and drilling on the PCB substrate in sequence;
[0043] B. After step A, firstly plate chemical copper on the entire PCB substrate, the thickness of chemical copper is 0.5um; then electroplate copper on the PCB substrate, the thickness of electroplated copper is 18um;
[0044] C. After step B, the PCB substrate surface is subjected to graphic transfer, and the graphic transfer includes lamination, one-time exposure and development treatment; the one-time exposure refers to the one-time exposure of the electroplated copper on the laminated PCB substrate surface by using line film. ; After exposure, the graphics transfer is completed through development treatment;
[0045] D. After step C, the PCB substrate is subjected to alkaline etching treatment, until the pH value of the PCB substrate is 8;
[0046] E. After th...
Embodiment 2
[0069] A method for directly etching a circuit on a negative film, comprising the following steps:
[0070] A. Carry out material cutting, edge grinding, filleting and drilling on the PCB substrate in sequence;
[0071] B. After step A, firstly plate chemical copper on the entire PCB substrate, the thickness of chemical copper is 0.8um; then electroplate copper on the PCB substrate, the thickness of electroplated copper is 20um;
[0072] C. After step B, the PCB substrate surface is subjected to graphic transfer, and the graphic transfer includes lamination, one-time exposure and development treatment; the one-time exposure refers to the one-time exposure of the electroplated copper on the laminated PCB substrate surface by using line film. ; After exposure, the graphics transfer is completed through development treatment;
[0073] D. After step C, the PCB substrate is subjected to alkaline etching treatment, until the pH value of the PCB substrate is 8;
[0074] E. After th...
Embodiment 3
[0087] A method for directly etching a circuit on a negative film, comprising the following steps:
[0088] A. Carry out material cutting, edge grinding, filleting and drilling on the PCB substrate in sequence;
[0089] B. After step A, firstly plate chemical copper on the entire PCB substrate, the thickness of chemical copper is 1um; then electroplate copper on the PCB substrate, the thickness of electroplated copper is 25um;
[0090] C. After step B, the PCB substrate surface is subjected to graphic transfer, and the graphic transfer includes lamination, one-time exposure and development treatment; the one-time exposure refers to the one-time exposure of the electroplated copper on the laminated PCB substrate surface by using line film. ; After exposure, the graphics transfer is completed through development treatment;
[0091] D. After step C, the PCB substrate is subjected to alkaline etching treatment, until the pH value of the PCB substrate is 9;
[0092] E. After the ...
PUM
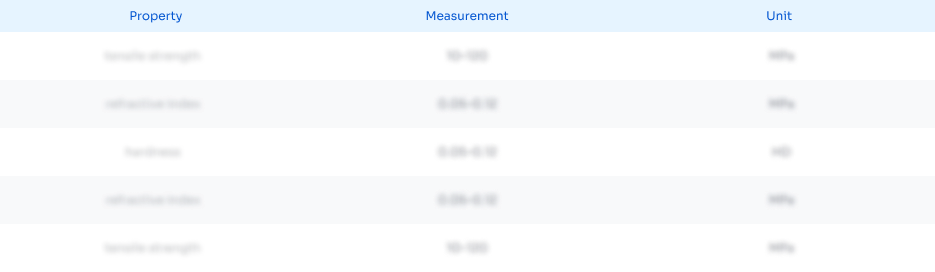
Abstract
Description
Claims
Application Information

- R&D
- Intellectual Property
- Life Sciences
- Materials
- Tech Scout
- Unparalleled Data Quality
- Higher Quality Content
- 60% Fewer Hallucinations
Browse by: Latest US Patents, China's latest patents, Technical Efficacy Thesaurus, Application Domain, Technology Topic, Popular Technical Reports.
© 2025 PatSnap. All rights reserved.Legal|Privacy policy|Modern Slavery Act Transparency Statement|Sitemap|About US| Contact US: help@patsnap.com