Assessment method for geometric errors of five-axis tool machine
A technology of tool machinery and geometric error, which is applied in the evaluation field that can measure and calculate the geometric error of five-axis tool machinery. And other issues
- Summary
- Abstract
- Description
- Claims
- Application Information
AI Technical Summary
Problems solved by technology
Method used
Image
Examples
Embodiment Construction
[0049] The technical contents and features of the present invention will be described in detail below in conjunction with the accompanying drawings through the enumerated embodiments, wherein:
[0050] figure 1 A schematic diagram of the model definition for the geometric error of the X linear motion axis of the present invention;
[0051] figure 2 A schematic diagram of the model definition for the geometric error of the C rotation axis of the present invention;
[0052] image 3 A schematic diagram of the coordinate system formed by erecting the R-test measuring tool on the five-axis tool machine for the present invention;
[0053] Figure 4 Utilize R-test gauge to measure the schematic diagram of gained assembly error for the present invention;
[0054] Figure 5 It is a comparison diagram of the error value after measurement and calculation by using the K4 path in a preferred embodiment of the present invention.
[0055] see figure 1 , the geometric error of tool ...
PUM
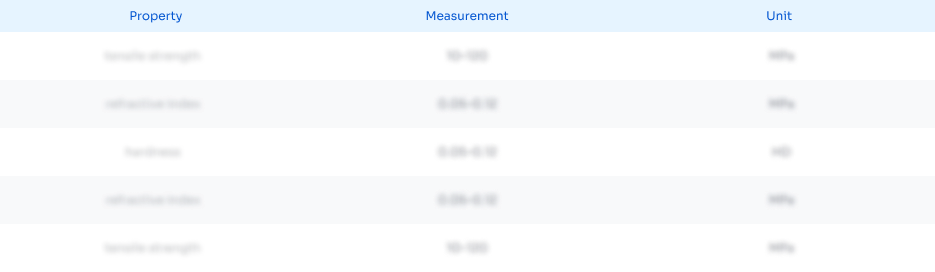
Abstract
Description
Claims
Application Information

- R&D
- Intellectual Property
- Life Sciences
- Materials
- Tech Scout
- Unparalleled Data Quality
- Higher Quality Content
- 60% Fewer Hallucinations
Browse by: Latest US Patents, China's latest patents, Technical Efficacy Thesaurus, Application Domain, Technology Topic, Popular Technical Reports.
© 2025 PatSnap. All rights reserved.Legal|Privacy policy|Modern Slavery Act Transparency Statement|Sitemap|About US| Contact US: help@patsnap.com