Method for manufacturing medium-density fiberboards
A production method and fiberboard technology, applied in the production field of medium density fiberboard, can solve the problems of environmental pollution, poor moisture resistance, rising production costs, etc., and achieve the effects of good physical and mechanical properties, lower production costs, and stable internal structure.
- Summary
- Abstract
- Description
- Claims
- Application Information
AI Technical Summary
Problems solved by technology
Method used
Image
Examples
Embodiment Construction
[0031] 1) Cutting: first cut the root and branch wood into 60×30×5mm wood chips according to the ratio, and at the same time take the screened sanding powder and the sawdust-like edge scraps according to the ratio for later use ;
[0032] 2) Cleaning: Wash the wood chips prepared from root and branch wood with water to remove the soil and other impurities attached to the surface of the wood chips, so as to ensure that the clean wood chips are transported to the next process;
[0033] 3) Cooking: Put the cleaned wood chips into the pre-cooking tank for preliminary softening, and then put them into the cooking tank for cooking to further soften them. The steam pressure in the cooking tank is 0.6-0.75 MPa, and the temperature is 145 —155°C, the cooking time of wood chips is 1-4 minutes; (In the actual production process, due to the changes of wood chip species, the change of loose and impurity ratio, and the change of product specifications, the cooking time, temperature and pres...
PUM
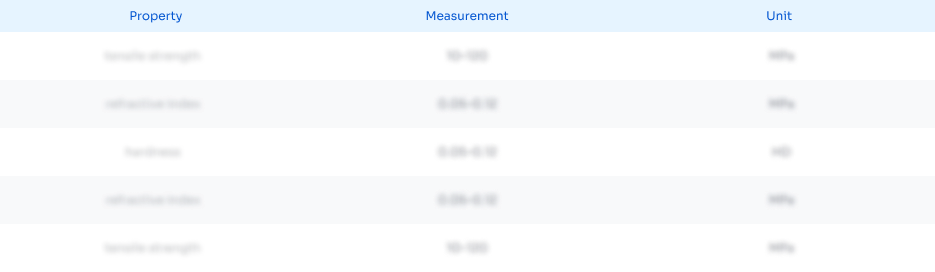
Abstract
Description
Claims
Application Information

- Generate Ideas
- Intellectual Property
- Life Sciences
- Materials
- Tech Scout
- Unparalleled Data Quality
- Higher Quality Content
- 60% Fewer Hallucinations
Browse by: Latest US Patents, China's latest patents, Technical Efficacy Thesaurus, Application Domain, Technology Topic, Popular Technical Reports.
© 2025 PatSnap. All rights reserved.Legal|Privacy policy|Modern Slavery Act Transparency Statement|Sitemap|About US| Contact US: help@patsnap.com