Method for preparing controllable viscosity hydroxyl-terminated polydimethylsiloxane
A dimethylsiloxane and hydroxyl-blocked technology, which is applied in the field of production of hydroxyl-blocked polydimethylsiloxane with controllable viscosity, can solve the problems of difficult control of viscosity and low laboratory reproducibility, and reduce the Cross-linking, the effect of uniform and transparent products
- Summary
- Abstract
- Description
- Claims
- Application Information
AI Technical Summary
Problems solved by technology
Method used
Examples
Embodiment 1
[0018] Hydrolyzate pretreatment: add 300g of hydrolyzate and 200g of water into a 500mL three-necked flask, stir for 30min at 50~75℃, add 20ppm of reagent A (reagent A is anion exchange resin and activated carbon), stir for 30min, then add 20ppm For reagent B, adjust the pH to 7.1, stop stirring, let stand, and separate to obtain the desired hydrolyzate.
[0019] Alkali glue preparation: add 150g DMC to a 250mL three-necked bottle, add 0.5g KOH after dehydration at 50-120°C, and polymerize at 130-150°C to obtain KOH alkali glue.
[0020] 107 Silicone rubber synthesis: Add the pretreated hydrolyzate into a 500mL reactor, raise the temperature, and dehydrate under vacuum. After the material is dehydrated, add 55ppm KOH alkali glue, heat up and polymerize at 100°C, and add phosphoric acid aqueous solution when the reaction system reaches the required viscosity. Neutralization. After neutralization, the system removes low molecules at a suitable temperature and vacuum until no fra...
Embodiment 2
[0022] Pretreatment of hydrolyzate: Add 300g of hydrolyzate and 200g of water into a 500mL three-necked flask, stir for 30min at a temperature of 50~75℃, add 20ppm of reagent A (reagent A is an anion exchange resin), stir for 30min, then add 30ppm of reagent B , adjust the pH=7.1, stop stirring, let it stand, and separate to obtain the desired hydrolyzate.
[0023] Alkali glue preparation: add 150g DMC to a 250mL three-necked bottle, add 0.5g KOH after dehydration at 50°C-120°C, and polymerize at 130-150°C to obtain KOH alkali glue.
[0024] 107 Silicone rubber synthesis: Add the pretreated hydrolyzate into a 500mL reactor, raise the temperature, and dehydrate under vacuum. After the material is dehydrated, add 55ppm KOH alkali glue, heat up and polymerize at 100°C, and add phosphoric acid aqueous solution when the reaction system reaches the required viscosity. Neutralization. After neutralization, the system removes low fractions at a suitable temperature and vacuum until no...
Embodiment 3
[0026] Pretreatment of hydrolyzate: Add 300g of hydrolyzate and 200g of water into a 500mL three-necked flask, stir for 30min at a temperature of 50~75°C, add 20ppm of reagent A (reagent A is silver nitrate), stir for 30min, then add 20ppm of reagent B, Adjust the pH to 7.1, stop stirring, let stand, and separate to obtain the desired hydrolyzate.
[0027] Alkali glue preparation: add 150g DMC to a 250mL three-necked bottle, add 0.5g KOH after dehydration at 50°C-120°C, and polymerize at 130-150°C to obtain KOH alkali glue.
[0028] 107 Synthesis of silicone rubber: Add the pretreated hydrolyzate into a 500mL reactor, raise the temperature, and dehydrate under vacuum. After the material is dehydrated, add 55ppm KOH alkali glue, heat up and polymerize at 120°C, and add phosphoric acid aqueous solution when the reaction system reaches the required viscosity. Neutralization. After neutralization, the system removes low fractions at a suitable temperature and vacuum until no fract...
PUM
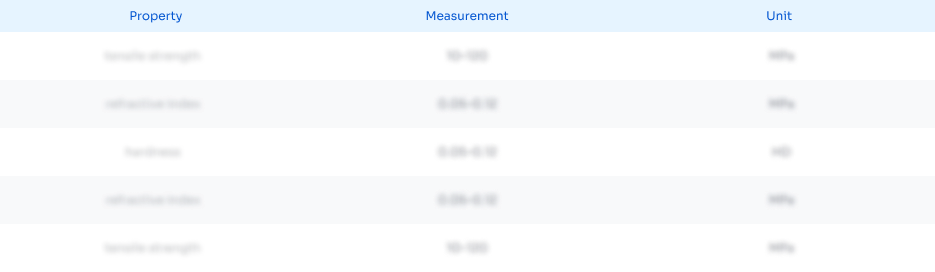
Abstract
Description
Claims
Application Information

- R&D
- Intellectual Property
- Life Sciences
- Materials
- Tech Scout
- Unparalleled Data Quality
- Higher Quality Content
- 60% Fewer Hallucinations
Browse by: Latest US Patents, China's latest patents, Technical Efficacy Thesaurus, Application Domain, Technology Topic, Popular Technical Reports.
© 2025 PatSnap. All rights reserved.Legal|Privacy policy|Modern Slavery Act Transparency Statement|Sitemap|About US| Contact US: help@patsnap.com