Drill rod wear-resisting belt flux-cored wire and manufacturing method thereof
A technology of a flux-cored welding wire and a manufacturing method, which is applied in the field of drilling, can solve problems such as affecting oil production and wear of drill pipes, and achieves the effects of improving service life and good anti-wear effect.
- Summary
- Abstract
- Description
- Claims
- Application Information
AI Technical Summary
Problems solved by technology
Method used
Image
Examples
Embodiment 1
[0028] 1) Roll the 15×0.4 (width 15mm, thickness 0.4mm) H08A cold-rolled steel strip into a U shape;
[0029] 2) Get 1.6 kg of chromium Cr powder, 0.4 kg of boron B, 0.04 kg of molybdenum Mo, 0.2 kg of nickel Ni, 0.06 kg of carbon C, and 16.84 kg of iron powder Fe, and fully mix them after passing through a 60-mesh sieve respectively; Mix in the powder mixer for 10 minutes to obtain the drug core powder;
[0030] 3) Add the drug core powder into the U-shaped H08A cold-rolled steel strip groove, the filling rate is 27% (that is, add powder to 27% of the space in the U-shaped groove), close the U-shaped groove, and wrap the drug powder in it , and then through drawing dies with diameters of 4.0mm, 3.0mm, 2.6mm, 2.4mm, 2.2mm, 2.0mm, 1.8mm, and 1.6mm, drawing and reducing the diameter one by one, and finally making the diameter reach 1.6mm. A drill pipe wear-resistant band flux-cored welding wire is obtained.
Embodiment 2
[0032] 1) Roll the 15×0.4 (width 15mm, thickness 0.4mm) H08A cold-rolled steel strip into a U shape;
[0033] 2) Take 1.66 kg of chromium powder, 0.48 kg of boron, 0.1 kg of molybdenum, 0.26 kg of nickel, 0.1 kg of carbon, and 17.4 kg of iron powder, pass through a 60-mesh sieve respectively, and mix in a powder mixer for 10 minutes to obtain the drug core powder;
[0034] 3) Add the drug core powder into the U-shaped H08A cold-rolled steel strip groove, the filling rate is 28wt%, close the U-shaped groove, wrap the drug powder in it, and then pass through the grooves with diameters: 4.0mm, 3.0mm, 2.6mm, 2.4mm, 2.2mm, 2.0mm, 1.8mm, 1.6mm wire drawing dies are drawn and reduced one by one, and finally the diameter reaches 1.6mm to obtain a drill pipe wear-resistant flux cored wire.
Embodiment 3
[0036] 1) Roll the 15×0.4 (width 15mm, thickness 0.4mm) H08A cold-rolled steel strip into a U shape;
[0037] 2) Get 1.76 kg of chromium powder, 0.56 kg of boron, 0.16 kg of molybdenum, 0.36 kg of nickel, 0.16 kg of carbon, and 17 kg of iron powder, pass through a 60-mesh sieve respectively, mix in a powder mixer for 10 minutes, and obtain the drug core powder;
[0038] 3) Put the drug core powder into the U-shaped H08A cold-rolled steel strip groove, the filling rate is 30wt%, close the U-shaped groove, wrap the drug powder in it, and then pass through the grooves with diameters: 4.0mm, 3.0mm, 2.6mm, 2.4mm, 2.2mm, 2.0mm, 1.8mm, 1.6mm wire drawing dies are drawn and reduced one by one, and finally the diameter reaches 1.6mm to obtain a drill pipe wear-resistant flux cored wire.
[0039]
[0040] Table 1
[0041] A drill pipe wear-resistant band flux-cored welding wire prepared in Examples 1, 2, and 3 was respectively surfacing welded on 40CrMo steel with a specification of...
PUM
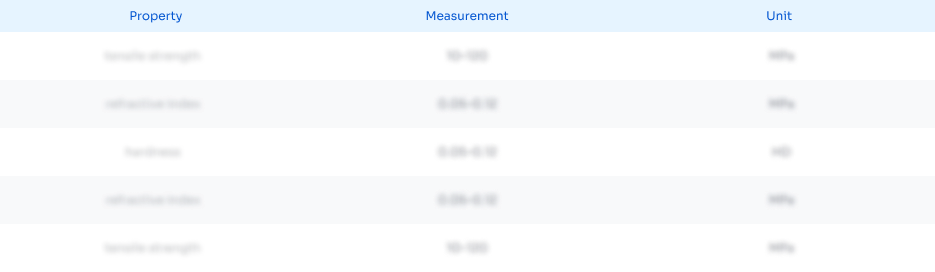
Abstract
Description
Claims
Application Information

- Generate Ideas
- Intellectual Property
- Life Sciences
- Materials
- Tech Scout
- Unparalleled Data Quality
- Higher Quality Content
- 60% Fewer Hallucinations
Browse by: Latest US Patents, China's latest patents, Technical Efficacy Thesaurus, Application Domain, Technology Topic, Popular Technical Reports.
© 2025 PatSnap. All rights reserved.Legal|Privacy policy|Modern Slavery Act Transparency Statement|Sitemap|About US| Contact US: help@patsnap.com