Method for machining small-cutting-in roughing-feed integral impeller rough slot
A technology of integral impeller and processing method, applied in metal processing equipment, manufacturing tools, details of milling machine equipment, etc., can solve problems such as prolonging processing time
- Summary
- Abstract
- Description
- Claims
- Application Information
AI Technical Summary
Problems solved by technology
Method used
Image
Examples
Embodiment 1
[0029] A rough grooving method for integral impellers with small depth of cut and high feed: use a special flying saucer milling cutter to process deep cavity grooves with a depth of 3-5 times the cutter radius, each cut depth is 1-4.5mm, and each tooth The dosage is 0.5-1mm;
[0030] The special flying saucer milling cutter meets the following requirements: it is composed of a cutter bar 1, a blade 2, and a fixing screw 3, and the blade 2 is positioned at the front end of the cutter bar 1 and is fixed on the cutter bar 1 by the fixing screw 3; The flying saucer milling cutter has three heads, the blade 2 has three pieces, and the blade 2 is triangular. Specifically, the main body profile of the blade 2 is a triangle, such as image 3 shown.
[0031]
[0032] In the rough grooving processing method of the integral impeller with small depth of cut and high feed, the depth of each cut is 1.5-4 mm, and the feed rate per tooth is preferably 0.55-0.8 mm.
[0033] In the rough g...
Embodiment 2
[0039] This embodiment is specifically implemented on the basis of embodiment 1, and the specific requirements different from embodiment 1 are as follows:
[0040] Titanium alloy deep cavity processing: The workpiece to be processed is an axial-flow integral impeller, and the processing part is the cavity between the blades. The processing depth is 170mm, and the tool is processed by a special milling cutter with a diameter of 40mm. The processing parameters are as follows: the cutting line speed is 63m / min, the feed rate per tooth is 0.5mm / tooth, the calculated tool speed is 500 rpm, the feed rate is 750mm / min, and the depth of cut for each layer is 1.2mm. The toolpath of the tool can be found in the appendix Figure 7 . Due to the large feed rate per tooth, the machining cooling method has a great impact on tool life. In order to prolong tool life, it must be equipped with an internal powerful cooling system.
[0041]
Embodiment 3
[0043] This embodiment is specifically implemented on the basis of embodiment 1, and the specific requirements different from embodiment 1 are as follows:
[0044] Die steel deep cavity processing: the workpiece to be processed is an extrusion die, the processing part is a cavity, the processing depth is 130mm, and the diameter of the tool is 40mm. Special milling cutter is used for processing. Processing example see attached Figure 8.
[0045] The processing parameters are as follows: the cutting line speed is 80m / min, the feed rate per tooth is 0.7mm / tooth, the calculated tool speed is 700 rpm, the feed rate is 140mm / min, and the depth of cut for each layer is 1.0mm. Due to the large feed rate per tooth, the machining cooling method has a great impact on tool life. In order to prolong tool life, it must be equipped with an internal powerful cooling system.
PUM
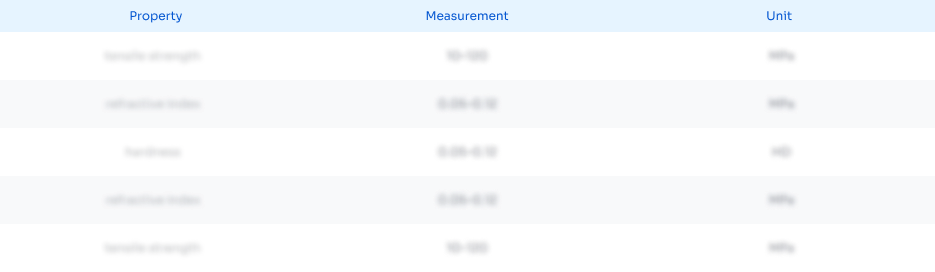
Abstract
Description
Claims
Application Information

- Generate Ideas
- Intellectual Property
- Life Sciences
- Materials
- Tech Scout
- Unparalleled Data Quality
- Higher Quality Content
- 60% Fewer Hallucinations
Browse by: Latest US Patents, China's latest patents, Technical Efficacy Thesaurus, Application Domain, Technology Topic, Popular Technical Reports.
© 2025 PatSnap. All rights reserved.Legal|Privacy policy|Modern Slavery Act Transparency Statement|Sitemap|About US| Contact US: help@patsnap.com