Total heat recovery type synthesis gas cooler with residue chamber
A synthesis gas cooler and total heat recovery technology, applied in the direction of joint combustion mitigation, combustible gas production, climate sustainability, etc. The problem of slag blocking the airflow channel and other problems can be achieved to increase the gas flow rate, reduce the production cost, and reduce the ash concentration.
- Summary
- Abstract
- Description
- Claims
- Application Information
AI Technical Summary
Problems solved by technology
Method used
Image
Examples
Embodiment 1
[0045] Such as figure 1 As shown, the gasification reaction chamber 3 is a vertical cylindrical space surrounded by the wall surface 4 of the reaction chamber. The fuel and gasification agent from the delivery pipeline 1 are sprayed into the reaction chamber through the burner 2, and the gasification reaction occurs, producing carbon monoxide and Synthesis gas with hydrogen as the main component. Most of the minerals in the fuel are in the molten liquid state and flow down the wall of the reaction chamber, and the other part is carried by the high-temperature syngas in the form of molten droplets. Outlets for synthesis gas and slag are located at the bottom of the reaction chamber. Next to the outlet at the bottom of the reaction chamber, a "U"-shaped slag chamber 6 is set. The "U"-shaped slag chamber is a U-shaped pipe surrounded by the wall surface 7 of the slag chamber. Refractory material" structure. The molten slag flowing out from the outlet at the bottom of the react...
Embodiment 2
[0049] Such as figure 2 As shown, the specific action principle of embodiment 2 is the same as that of embodiment 1, except that after the gas enters the syngas cooler, since the synthesizer cooler can be designed as different gas flow directions according to needs, in this embodiment, the gas flows downward flow, and the wall of the syngas cooler is a membrane water wall structure. In the syngas cooler, a certain number and form of radiation heating surfaces 14 and convective heating surfaces 15 can be arranged in sequence along the flow direction, and finally the syngas cooled to a certain temperature is drawn out from the lower gas outlet of the syngas cooler.
PUM
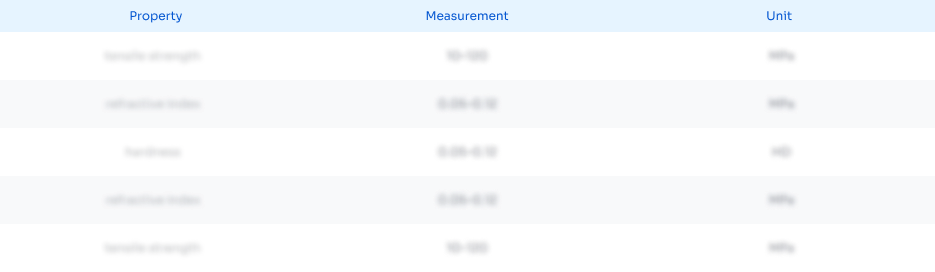
Abstract
Description
Claims
Application Information

- Generate Ideas
- Intellectual Property
- Life Sciences
- Materials
- Tech Scout
- Unparalleled Data Quality
- Higher Quality Content
- 60% Fewer Hallucinations
Browse by: Latest US Patents, China's latest patents, Technical Efficacy Thesaurus, Application Domain, Technology Topic, Popular Technical Reports.
© 2025 PatSnap. All rights reserved.Legal|Privacy policy|Modern Slavery Act Transparency Statement|Sitemap|About US| Contact US: help@patsnap.com