Oil absorption material using cellulose as base and preparation method thereof
An oil-absorbing material and cellulose technology, which is applied in the field of absorbing materials for marine oil spills and their preparation, can solve the problems of producing harmful gases, high transportation costs, and small oil absorption, and achieve lipophilic and hydrophobic performance and dimensional stability. Improve, rich in resources, good oil absorption effect
- Summary
- Abstract
- Description
- Claims
- Application Information
AI Technical Summary
Problems solved by technology
Method used
Image
Examples
Embodiment 1
[0025] (1) Cut the corn stalks into 10-20cm long pieces and soak them in boiling water at 100°C for 48 hours, then dry them in the sun to remove the moisture on the surface of the stalks, and dry them in a vacuum oven at 80°C for 16 hours.
[0026] (2) The dried corn stalks were pretreated by the ammonia circulation blasting method, the reaction temperature was 70°C, the reaction pressure was 1.8Mpa, the maintenance pressure time was 5min, and the flow rate of ammonia water was 2L / min. Specifically, the corn stalks were put into Into the ammonia explosion reactor and add deionized water, after closing the valve, slowly feed ammonia water into the system, use steam to heat to the predetermined reaction temperature, and use the ammonia pump to make the ammonia water flow in the pump-ammonia explosion reactor- The ammonia liquid buffer tank circulates and flows. When the predetermined reaction time is reached, the starting ball valve is opened, and the pressure is released instant...
Embodiment 2
[0033] (1) Cut corn stalks into 10-20cm long pieces and soak them in boiling water at 100°C for 48 hours, then dry them in the sun to remove moisture from the surface of the stalks, and dry them in a vacuum oven at 60°C for 16 hours.
[0034] (2) In step 2, the dried corn stalks are pretreated by the ammonia water circulation blasting method. The reaction temperature is 90°C, the reaction pressure is 0.9Mpa, the pressure maintenance time is 9min, and the ammonia water flow rate is 1L / min. Specifically, refer to Master's degree thesis "Research on the Pretreatment Effect of Ammonia Water Blasting Method on Corn Stalks", Zhang Chao, June 2010.
[0035] (3) Soak the straw treated in step (2) in a mixture of benzene and ethanol with a volume ratio of 2:1 for 20 hours, filter it out, and dry it in a vacuum drying oven at 60°C for 6 hours.
[0036] (4) Place the dried corn stalks in distilled water, heat and pretreat in a water bath at 70°C for 5 hours, then cool and filter.
[003...
Embodiment 3
[0041] (1) Cut corn stalks into 10-20cm long pieces and soak them in boiling water at 100°C for 48 hours, then dry them in the sun to remove moisture from the surface of the stalks, and dry them in a vacuum oven at 60°C for 16 hours.
[0042] (2) In step 2, the dried corn stalks were pretreated by the ammonia circulation blasting method, the reaction temperature was 80°C, the reaction pressure was 1.2Mpa, the pressure maintenance time was 7min, and the ammonia flow rate was 1.5L / min. Specifically, Refer to the master's degree thesis "Research on the Pretreatment Effect of Ammonia Water Blasting Method on Corn Stalks", Zhang Chao, June 2010.
[0043] (3) Soak the straw treated in step (2) in a mixture of benzene and ethanol with a volume ratio of 2:1 for 20 hours, filter it out, and dry it in a vacuum drying oven at 60°C for 6 hours.
[0044] (4) Place the dried corn stalks in distilled water, heat and pretreat in a water bath at 70°C for 5 hours, then cool and filter.
[0045...
PUM
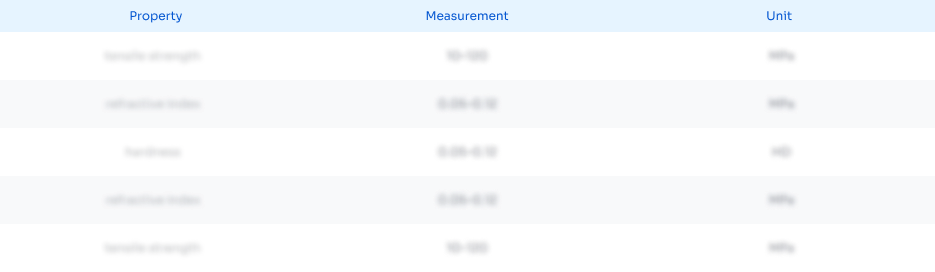
Abstract
Description
Claims
Application Information

- R&D
- Intellectual Property
- Life Sciences
- Materials
- Tech Scout
- Unparalleled Data Quality
- Higher Quality Content
- 60% Fewer Hallucinations
Browse by: Latest US Patents, China's latest patents, Technical Efficacy Thesaurus, Application Domain, Technology Topic, Popular Technical Reports.
© 2025 PatSnap. All rights reserved.Legal|Privacy policy|Modern Slavery Act Transparency Statement|Sitemap|About US| Contact US: help@patsnap.com