Multi-layer co-sintered lamination stackable chip resistor and manufacturing method thereof
A chip resistor, stacking technology, used in resistor manufacturing, resistors, trimmer resistors, etc., can solve the problems of efficient use, complicated locking and multi-layer co-firing, saving time and eliminating stacking procedures. Effect
- Summary
- Abstract
- Description
- Claims
- Application Information
AI Technical Summary
Problems solved by technology
Method used
Image
Examples
Embodiment Construction
[0055] The multilayer co-fired multilayer stacked chip resistor and its manufacturing method provided by the present invention realize a multilayer stacked chip resistor structure by the multilayer cofiring technology.
[0056] The technical means adopted by the present invention to solve the problems of the known technologies is to firstly prepare a porcelain slurry including a solvent, a binder and a dispersant, and attach the porcelain slurry to the surface of a carrier film to form a ceramic film, and then A plurality of layers of the ceramic film are laminated to form a ceramic matrix with a predetermined thickness. Then a resistance layer is formed on the surface of the ceramic substrate, the ends of the resistance layer extend in a horizontal direction respectively to form terminal connection ends, and the ceramic film is formed on the surface of the resistance layer.
[0057] repeating the first two steps several times to form a monolithic stacked resistance structure ...
PUM
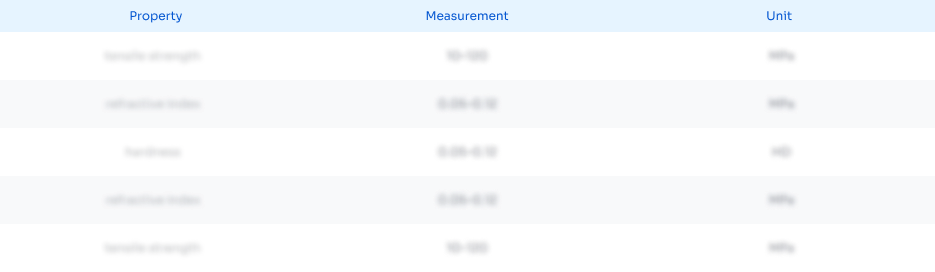
Abstract
Description
Claims
Application Information

- R&D
- Intellectual Property
- Life Sciences
- Materials
- Tech Scout
- Unparalleled Data Quality
- Higher Quality Content
- 60% Fewer Hallucinations
Browse by: Latest US Patents, China's latest patents, Technical Efficacy Thesaurus, Application Domain, Technology Topic, Popular Technical Reports.
© 2025 PatSnap. All rights reserved.Legal|Privacy policy|Modern Slavery Act Transparency Statement|Sitemap|About US| Contact US: help@patsnap.com