Synthetic resin for water-soluble printing ink and preparation method thereof
A synthetic resin and water-soluble technology, which can be used in inks, applications, household utensils, etc., can solve the problems of slow drying, volatile pollution, poor wetting and dispersibility of pigments, etc., and achieve convenient and easy raw materials, low preparation costs, and high adhesion strength Effect
- Summary
- Abstract
- Description
- Claims
- Application Information
AI Technical Summary
Problems solved by technology
Method used
Examples
Embodiment 1
[0028] The amount of raw materials used in the preparation of synthetic resin for water-soluble ink: 210 kg of turpentine, 290 kg of butyl acrylate, 70 kg of methyl methacrylate, 350 kg of vinyl acetate, 50 kg of hydroxyethyl acrylate, 30 kg of acrylic acid, persulfuric acid Potassium 4.8 kg, catalyst: 5.5 kg of a mixture of benzyl chloride and aluminum chloride (mass ratio 1: 1).
[0029] The concrete preparation steps of synthetic resin for water-soluble ink are as follows:
[0030] 1. Terpene Prepolymer Preparation
[0031] [1] Catalyst is joined in the mixed solvent that is made up of 36kg ethyl acetate and 4kg toluene, mixes;
[0032] [2] turpentine and the mixed solvent that is made up of 162kg ethyl acetate and 18kg toluene are dropped into reactor, stir;
[0033] [3] When the temperature of the reactor reaches 5°C, add the catalyst solution obtained in step [1] into the reactor, keep the temperature of the reactor not exceeding 15°C, and react for 3 hours;
[0034] ...
Embodiment 2
[0040] The amount of raw materials used in the preparation of synthetic resin for water-soluble ink: 180 kg of turpentine, 380 kg of butyl acrylate, 100 kg of methyl methacrylate, 270 kg of vinyl acetate, 40 kg of glycidyl acrylate, 30 kg of acrylic acid, persulfuric acid Potassium 5.1 kg, catalyst: 4.8 kg of a mixture of benzyl chloride and aluminum chloride (mass ratio 1: 1).
[0041] The concrete preparation steps of synthetic resin for water-soluble ink are as follows:
[0042] 1. Terpene Prepolymer Preparation
[0043] [1] Catalyst is joined in the mixed solvent that is made up of 36kg ethyl acetate and 4kg toluene, mixes;
[0044] [2] turpentine and the mixed solvent that is made up of 135kg ethyl acetate and 18kg toluene are dropped into reactor, stir;
[0045] [3] When the temperature of the reactor reaches 10°C, add the catalyst solution obtained in step [1] into the reactor, keep the temperature of the reactor not exceeding 15°C, and react for 3 hours;
[0046] [4...
Embodiment 3
[0052]The amount of raw materials used in the preparation of synthetic resin for water-soluble ink: 190 kg of turpentine, 330 kg of butyl acrylate, 80 kg of styrene, 330 kg of vinyl acetate, 30 kg of methacrylic acid, 40 kg of tertiary vinyl ester (Shell) , 5.2 kg of potassium persulfate, catalyst: 4.8 kg of a mixture of benzyl chloride and aluminum chloride (mass ratio 1: 1).
[0053] The concrete preparation steps of synthetic resin for water-soluble ink are as follows:
[0054] 1. Terpene Prepolymer Preparation
[0055] [1] Catalyst is joined in the mixed solvent that is made up of 36kg ethyl acetate and 4kg toluene, mixes;
[0056] [2] turpentine and the mixed solvent that is made up of 144kg ethyl acetate and 16kg toluene are dropped into reactor, stir;
[0057] [3] When the temperature of the reactor reaches 10°C, add the catalyst solution obtained in step [1] into the reactor, keep the temperature of the reactor not exceeding 15°C, and react for 3 hours;
[0058] [4]...
PUM
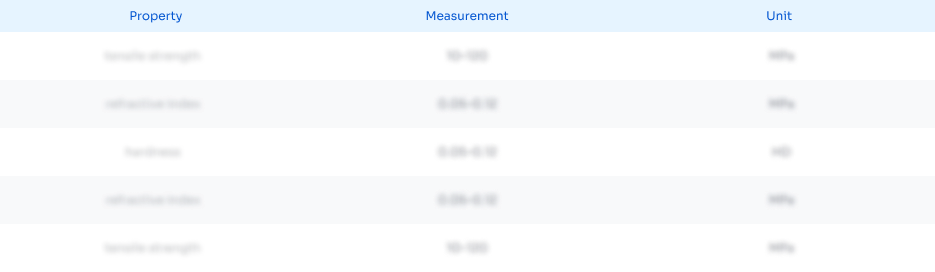
Abstract
Description
Claims
Application Information

- Generate Ideas
- Intellectual Property
- Life Sciences
- Materials
- Tech Scout
- Unparalleled Data Quality
- Higher Quality Content
- 60% Fewer Hallucinations
Browse by: Latest US Patents, China's latest patents, Technical Efficacy Thesaurus, Application Domain, Technology Topic, Popular Technical Reports.
© 2025 PatSnap. All rights reserved.Legal|Privacy policy|Modern Slavery Act Transparency Statement|Sitemap|About US| Contact US: help@patsnap.com