Preparation method for modified foundry furan resin
A furan resin and modification technology, which is applied in casting molding equipment, casting molds, manufacturing tools, etc., can solve problems affecting the health of casting personnel, and achieve the effects of easy control and industrialization, low price, and a wide range of sugar sources
- Summary
- Abstract
- Description
- Claims
- Application Information
AI Technical Summary
Problems solved by technology
Method used
Image
Examples
Embodiment 1
[0038] Add 100g sucrose to 40g water until dissolved, then add 5g concentrated hydrochloric acid and 0.1g phenol, stir and heat up to 70°C, react for 10h, cool down to 30°C, adjust the pH value to 8.5 with 30% sodium hydroxide, add 0.1g The formaldehyde was reacted at 60°C for 3 hours, and then 40 g was dehydrated to obtain a brown-red viscous liquid.
[0039] According to the corresponding steps of the comparative example, under the conditions of steps (1) to (3) unchanged, in step (4), take 5 g of the above-mentioned brown-red viscous liquid to replace 5 g of furfuryl alcohol in step (4) of the comparative example (the total amount of raw materials 5% by weight), the raw materials actually participating in the reaction are 35g furfuryl alcohol, 5g brownish-red viscous liquid and 0.85g silane coupling agent, and other conditions remain unchanged to obtain a modified furan resin for casting, and its properties are shown in Table 1.
Embodiment 2
[0041] Add 100g sucrose to 75g water until dissolved, then add 15g concentrated phosphoric acid and 13.75g phenol, stir and heat up to 90°C, react for 2h, cool down to 60°C, adjust the pH value to 8.5 with 30% sodium hydroxide, add 3g of Formaldehyde was reacted at 90°C for 1 hour, and then 85 g was dehydrated to obtain a brown-black viscous liquid.
[0042] According to the corresponding steps of the comparative example, under the conditions of steps (1) to (3) unchanged, in step (4), take 10 g of the above-mentioned brown-black viscous liquid to replace 10 g of furfuryl alcohol in the step (4) of the comparative example (the total amount of raw materials 10% of the weight), the actual raw materials participating in the reaction are 30g furfuryl alcohol, 10g brown-black viscous liquid and 0.85g silane coupling agent, and other conditions remain unchanged to obtain a modified furan resin for casting, and its properties are shown in Table 1.
Embodiment 3
[0044] Add 100g sucrose to 80g water until dissolved, then add 20g concentrated nitric acid, 10g phenol and 5g hydroquinone, stir and heat up to 90°C, react for 2h, cool down to 60°C, adjust the pH value to 9.0, add 5g of formaldehyde, heat up to 90°C for 2 hours, then dehydrate 85g to obtain a brown-black viscous liquid.
[0045] According to the corresponding steps of the comparative example, under the condition that the steps (1) to (3) remain unchanged, in the step (4), take 20 g of the above-mentioned brown-black viscous liquid to replace 20 g of furfuryl alcohol in the step (4) of the comparative example (the total amount of raw materials 20% by weight), the actual raw materials that participated in the reaction were 20g furfuryl alcohol, 20g brown-black viscous liquid and 0.85g silane coupling agent, and other conditions were unchanged to obtain a modified furan resin for casting, and its properties are shown in Table 1.
PUM
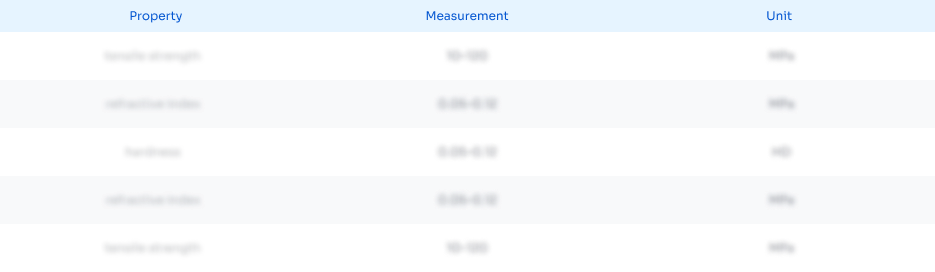
Abstract
Description
Claims
Application Information

- R&D Engineer
- R&D Manager
- IP Professional
- Industry Leading Data Capabilities
- Powerful AI technology
- Patent DNA Extraction
Browse by: Latest US Patents, China's latest patents, Technical Efficacy Thesaurus, Application Domain, Technology Topic, Popular Technical Reports.
© 2024 PatSnap. All rights reserved.Legal|Privacy policy|Modern Slavery Act Transparency Statement|Sitemap|About US| Contact US: help@patsnap.com