Needle rod eccentric pin of sewing machine and manufacturing method thereof
An eccentric pin and sewing machine technology, applied in the field of mechanical processing, can solve the problems of high processing cost and unstable quality, and achieve the effects of low cost, stable product quality and convenient operation
- Summary
- Abstract
- Description
- Claims
- Application Information
AI Technical Summary
Problems solved by technology
Method used
Image
Examples
Embodiment 1
[0027] Put the zinc alloy whose composition is shown in Example 1 in Table 1 into the melting furnace, and raise the temperature to 315° C. in the atmosphere to melt the zinc alloy into molten metal. At room temperature, the zinc alloy metal is hydraulically injected into an existing common mold for producing eccentric pins and left to stand, and then the metal is hydraulically cast into an eccentric pin blank at a pressure of 98Mpa. The blank is then vibrated and ground into a needle bar eccentric pin.
Embodiment 2
[0029] Put the zinc alloy whose composition is shown in Example 2 in Table 1 into the melting furnace, and raise the temperature to 325° C. in the atmosphere to melt the zinc alloy into molten metal. At room temperature, the zinc alloy metal is hydraulically injected into the existing common mold for manufacturing eccentric pins and left to stand, and then the metal is hydraulically cast into a needle bar eccentric pin blank at a pressure of 103Mpa. The blank is then vibrated and ground into a needle bar eccentric pin.
Embodiment 3
[0031] Put the zinc alloy whose composition is shown in Example 3 in Table 1 into the melting furnace, and raise the temperature to 310° C. in the atmosphere to melt the zinc alloy into molten metal. At room temperature, the zinc alloy metal is hydraulically injected into an existing common mold for manufacturing eccentric pins and left to stand, and then the metal is hydraulically cast into a needle bar eccentric pin blank at a pressure of 95Mpa. The blank is then vibrated and ground into a needle bar eccentric pin.
PUM
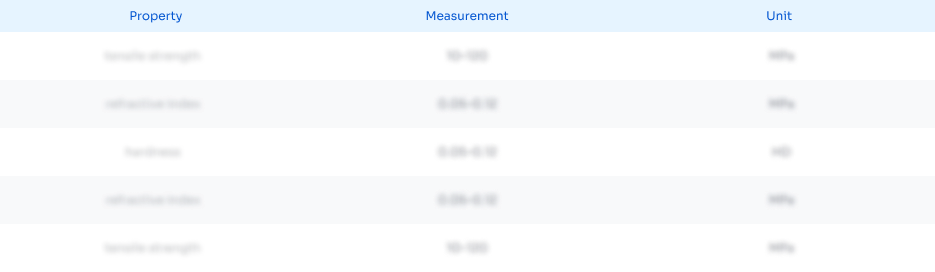
Abstract
Description
Claims
Application Information

- Generate Ideas
- Intellectual Property
- Life Sciences
- Materials
- Tech Scout
- Unparalleled Data Quality
- Higher Quality Content
- 60% Fewer Hallucinations
Browse by: Latest US Patents, China's latest patents, Technical Efficacy Thesaurus, Application Domain, Technology Topic, Popular Technical Reports.
© 2025 PatSnap. All rights reserved.Legal|Privacy policy|Modern Slavery Act Transparency Statement|Sitemap|About US| Contact US: help@patsnap.com