Method for testing crack sensitivity of precision steel casting and test model thereof
A technology of crack sensitivity and test model, applied in the field of metal casting, can solve the problems of single structure, unable to achieve sufficient and reasonable, crack sensitivity can not be reflected at the same time, etc., to achieve the effect of low cost and reduce crack defects
- Summary
- Abstract
- Description
- Claims
- Application Information
AI Technical Summary
Problems solved by technology
Method used
Image
Examples
Embodiment 1
[0039] According to the material components designed in Table 1 and the pouring process parameters shown in Table 2, the test model is manufactured and pressed according to the normal investment casting process—pressed wax mold—set tree—shell making—demoulding— — roasting — melting and casting — cleaning;
[0040] Select 30 cleaned test models, and use cast steel shots with a hardness of 40HRC for shot blasting. Grease, dirt, scale, rust, corrosion products, oxides and others are not allowed to exist on the surface of the cleaned test models impurities;
[0041] After the shot blasting treatment, the surface of the test model, including the fillet transition, is cleaned with a colored crack cleaner;
[0042] Spray the crack observation part of the model with colored penetrant and keep it wet for 5 minutes;
[0043] Wipe off the excess penetrant on the surface of the test model, and clean the observation part with cleaning agent;
[0044] After the surface is dry, spray a colo...
Embodiment 2
[0054] According to the material components designed in Table 4, the pouring process parameters are the same as in Example 1, and the test model is manufactured according to the normal investment casting process. Pressing the mold - pressing the wax mold - forming the tree - making the shell - demoulding - — roasting — melting and casting — cleaning;
[0055] (2) The cleaned test model is shot blasted with cast steel shots with a hardness of 45HRC. Grease, dirt, scale, rust, corrosion products, oxides and other impurities are not allowed to exist on the surface of the cleaned test model;
[0056] (3) After the shot peening treatment is completed, the surface of the test model, including the fillet transition, is cleaned with a colored crack cleaner;
[0057] (4) Spray the observation part of the test model with colored penetrant and keep it moist for 10 minutes;
[0058] (5) Wipe off the excess penetrant on the surface of the test model, and clean the observation part with cl...
Embodiment 3
[0067] According to the material components designed in Table 6, the pouring process parameters are the same as in Example 1, and the manufacturing of the test model is carried out according to the normal investment casting process. Pressing the mold - pressing the wax mold - forming the tree - making the shell - demoulding - — roasting — melting and casting — cleaning;
[0068] (2) The cleaned test model is shot blasted with cast steel shots with a hardness of 50HRC. Grease, dirt, scale, rust, corrosion products, oxides and other impurities are not allowed to exist on the surface of the cleaned test model;
[0069] (3) After the shot peening treatment is completed, the surface of the test model, including the fillet transition, is cleaned with a colored crack cleaner;
[0070] (4) Spray the observation part of the test model with colored penetrant and keep it moist for 8 minutes;
[0071] (5) Wipe off the excess penetrant on the surface of the test model, and clean the obser...
PUM
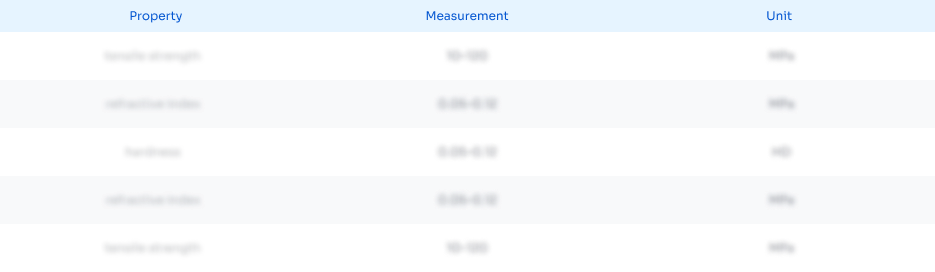
Abstract
Description
Claims
Application Information

- R&D
- Intellectual Property
- Life Sciences
- Materials
- Tech Scout
- Unparalleled Data Quality
- Higher Quality Content
- 60% Fewer Hallucinations
Browse by: Latest US Patents, China's latest patents, Technical Efficacy Thesaurus, Application Domain, Technology Topic, Popular Technical Reports.
© 2025 PatSnap. All rights reserved.Legal|Privacy policy|Modern Slavery Act Transparency Statement|Sitemap|About US| Contact US: help@patsnap.com